How Autonomous Maintenance Drives Safety in Metal Manufacturing
Whether you're managing high-capacity press brakes or automated tube bending machines, workplace safety is paramount in metal manufacturing environments, the following Autonomous Maintenance (AM) guidance will provide insights to
enhance workplace safety, reduce hazards, and empower operators to take ownership of equipment care.
Why Safety Matters in Metal Manufacturing
Metal manufacturing facilities, such as pipe and tube plants serving construction and energy industries, face unique challenges related to workplace safety. Heavy machinery, high temperatures, and complex equipment create risks that require proactive strategies to mitigate. This is where Autonomous Maintenance (AM) comes into play.
Key Benefits of Autonomous Maintenance for Safety:
- Proactive Hazard Prevention: Operators identify and address issues before they escalate.
- Improved Equipment Reliability: Routine upkeep minimizes unexpected failures that could lead to accidents
- Enhanced Operator confidence: Empowered operators take ownership of safety
The Role of AM in Total Productive Maintenance (TPM)
Autonomous Maintenance (AM) is one of the eight pillars of Total Productive Maintenance (TPM). It focuses on empowering operators to perform routine maintenance tasks such as cleaning, inspections, and minor repairs. By fostering a culture of shared responsibility between operators and maintenance teams, AM ensures that equipment operates safely and efficiently.
How AM Improves Safety:
- Early Problem Detection: Operators spot issues like leaks or wear during routine checks.
- Consistent Equipment Care: Regular cleaning and lubrication prevent deterioration.
- Structured Training: Operators gain the skills needed to maintain equipment safely
Real-Life Example: Pipe and Tube Plant in Bethlehem
At a pipe and tube manufacturing plant in Bethlehem, Pennsylvania, an operator noticed unusual vibrations during routine Autonomous Maintenance checks on a tube bending machine. Here’s how AM principles prevented a potential hazard:
- The operator inspected the hydraulic system and discovered a loose fitting causing fluid leakage—a potential slip hazard.
- Tightened the fitting and cleaned the area thoroughly.
- Checked the machine’s safety guards for proper alignment.
These proactive actions not only prevented a workplace accident but also avoided damage to critical components that could have led to downtime. By empowering operators through AM training, the plant ensured safer operations and uninterrupted production schedules.
The Impact of AM on Workplace Safety
According to the Kaizen institute "AM contributes to creating a safer work environment. Operators involved in maintenance activities become more aware of the risks and necessary safety measures. This results in a reduction in accidents and equipment-related injuries."
Driving Safety with TPM
Operations leaders across the metal manufacturing industry are increasingly adopting technologies that support TPM initiatives like Autonomous Maintenance. By empowering operators to take ownership of routine maintenance tasks, manufacturers can reduce workplace hazards, improve reliability, and boost productivity.
Learn More
For more insights into TPM strategies and their benefits for workplace safety, visit:
SafetyCulture’s Guide to Total Productive Maintenance
Camcode’s Overview of Autonomous Maintenance
MaintainX’s Beginner’s Guide to Autonomous Maintenance
And that’s your Corvex Connected Workforce Quick Take!
Contact Corvex
Connect Your Workforce Today
Contact Us
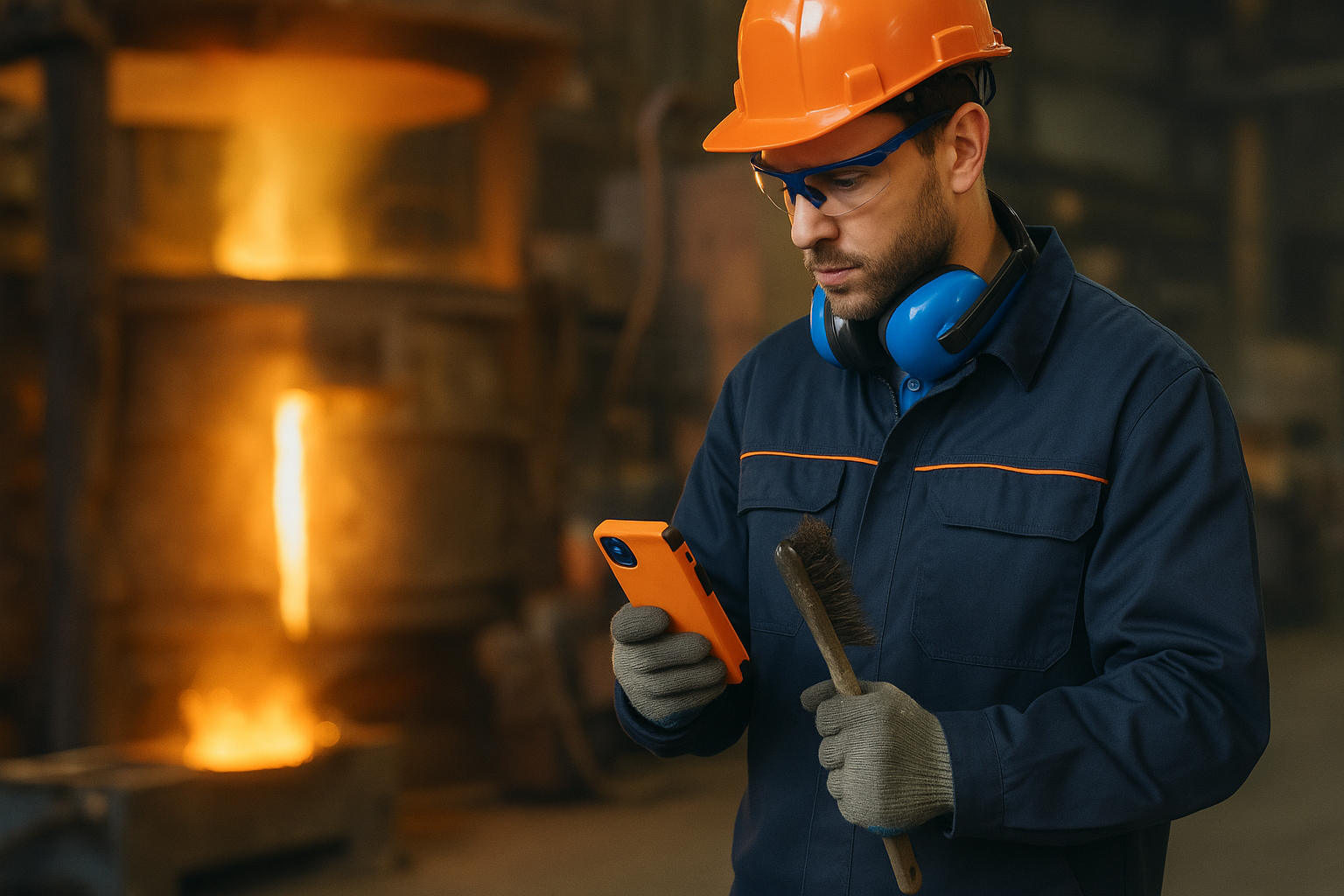
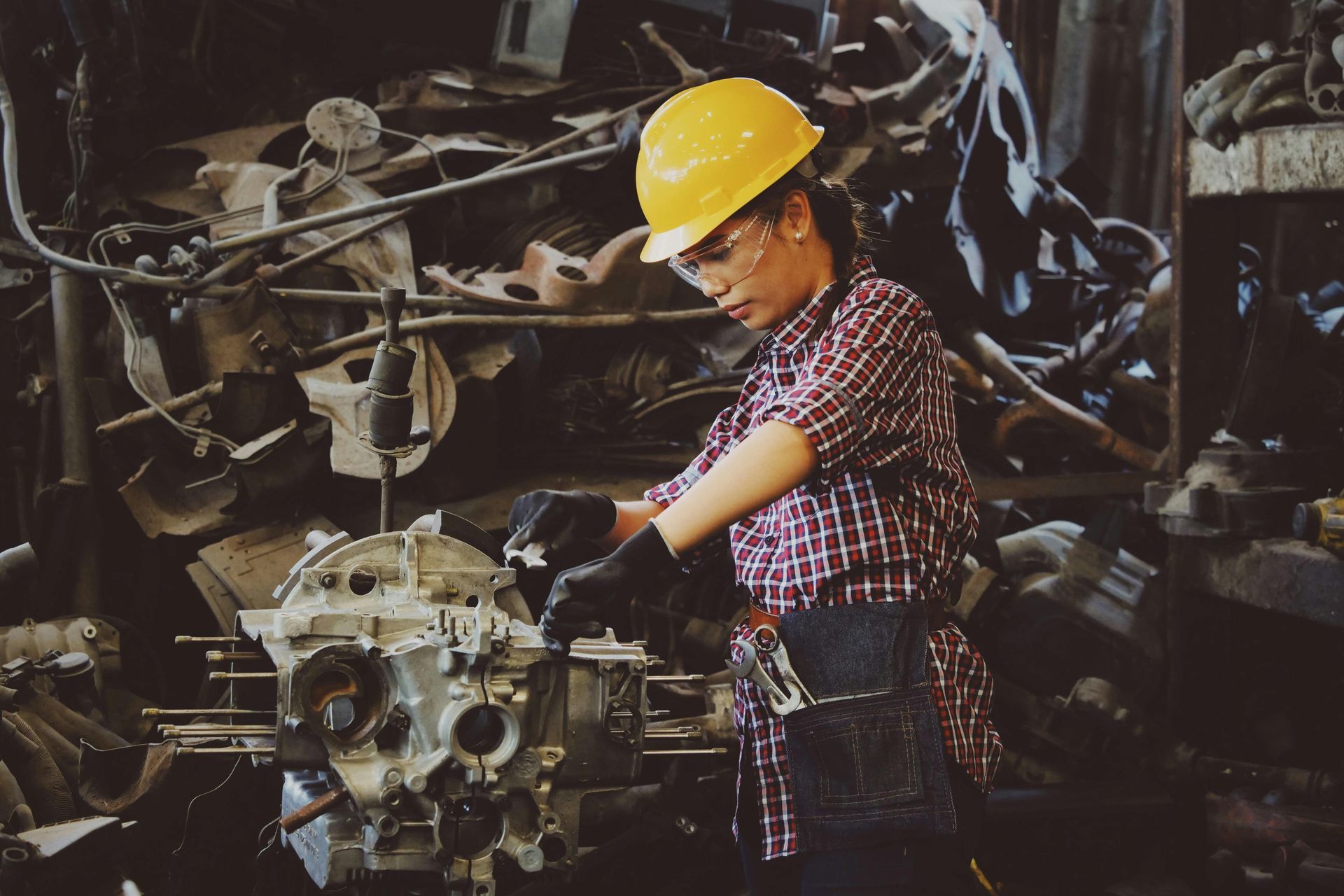
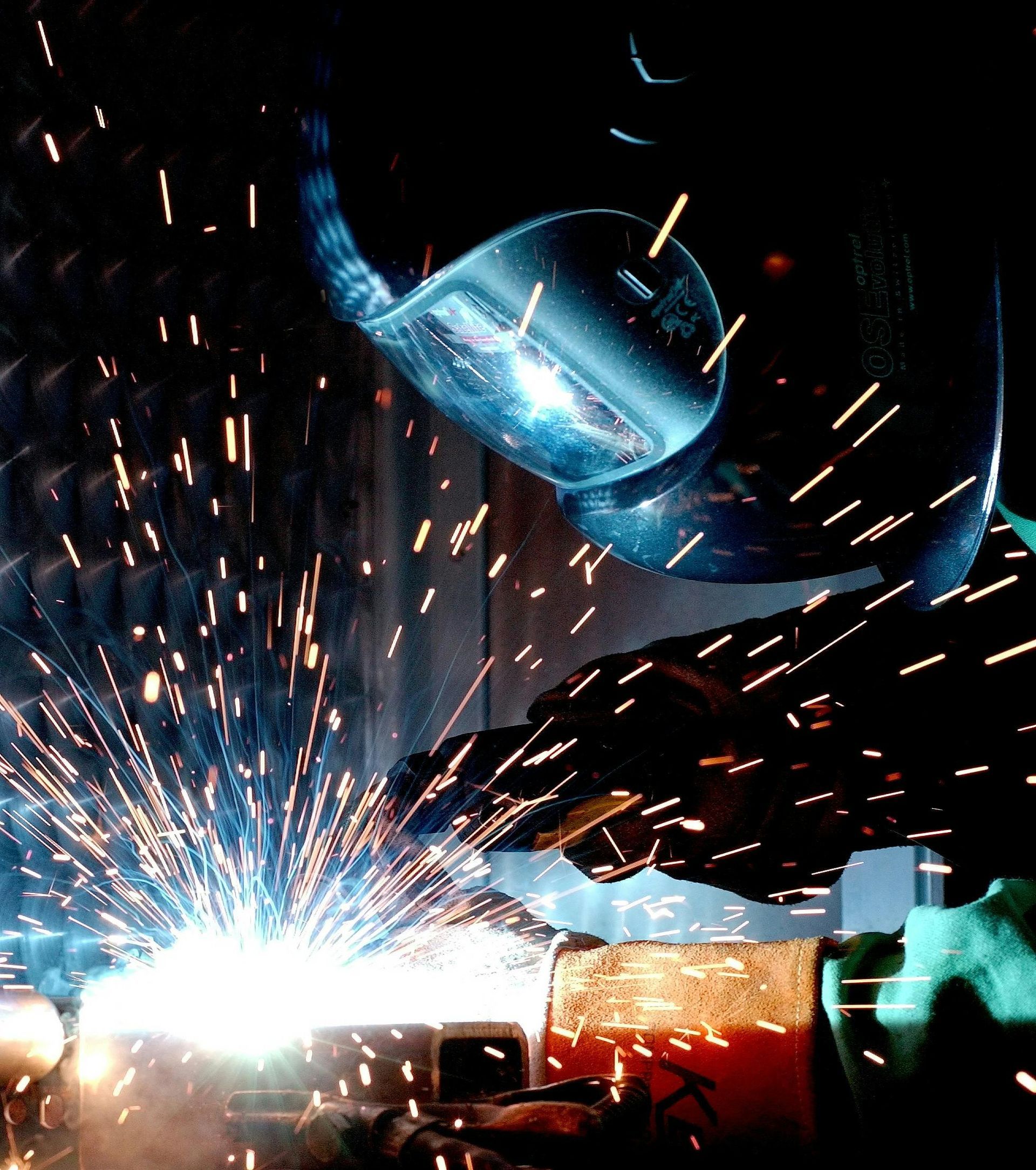