Autonomous Maintenance vs. Planned Maintenance: Unlocking the Power of TPM in Metal Manufacturing
The Foundations of Autonomous Maintenance and Planned Maintenance
Autonomous Maintenance (AM) empowers operators to take ownership of routine equipment care, such as cleaning, lubrication, and minor repairs. This proactive approach fosters a culture of accountability, reduces downtime, and extends equipment lifespan. On the other hand, Planned Maintenance (PM) involves scheduled interventions by maintenance teams to prevent breakdowns and address wear and tear through inspections, repairs, and replacements.
Key Benefits of Autonomous Maintenance:
- Reduced Downtime: Operators identify potential issues early, preventing unplanned stoppages
- Improved Equipment Lifespan: Routine care prevents excessive wear
- Enhanced Operator Productivity: Empowered operators take pride in their role
Key Benefits of Autonomous Maintenance:
- Proactive Problem Prevention: Scheduled downtime avoids costly disruptions
- Focus on Complex Repairs: Dedicated teams handle advanced maintenance tasks
How AM and PM Work Together in TPM
While AM focuses on empowering operators for daily care tasks, PM ensures that deeper issues are addressed systematically. Together, these strategies create a balanced approach to equipment reliability and operational efficiency. Operators learn to identify emerging issues before they escalate.
Real-Life Success Story: Casting Plant in Milwaukee
At a casting plant in Milwaukee, Wisconsin, a CNC machining operator trained in Autonomous Maintenance noticed coolant levels dropping during routine checks. Following AM principles:
- The operator inspected the machine independently
- Identified a leaking hose
- Replaced the hose and cleaned the area thoroughly
This proactive effort prevented a coolant spill that could have created slip hazards and ensured uninterrupted machine operation without external intervention. By combining AM with PM strategies, the plant achieved safer operations and improved productivity.
The Transformative Impact of Autonomous Maintenance and Planned Maintenance
According to the Kaizen Institute AM results in greater equipment reliability, reduction of failures, increased lifespan, reduced downtime, and overall improvement in operational performance. Planned maintenance aims to maximize equipment availability through efficient planning of maintenance activities.
When combined—AM empowering operators to detect early issues and PM ensuring systematic upkeep—these strategies yield powerful synergies that significantly enhance equipment reliability, reduce disruptions, and elevate productivity.
Drive Excellence with TPM
Leaders in casting operations are increasingly turning to TPM initiatives like Autonomous Maintenance to enhance safety, reliability, and productivity. By empowering operators through AM and complementing it with PM strategies, metal manufacturing plants can unlock unparalleled efficiency and resilience.
Learn More
For more insights into TPM strategies and their benefits, visit Lean Production’s TPM Framework
And that’s your Corvex Connected Workforce Quick Take!
Contact Corvex
Connect Your Workforce Today
Contact Us
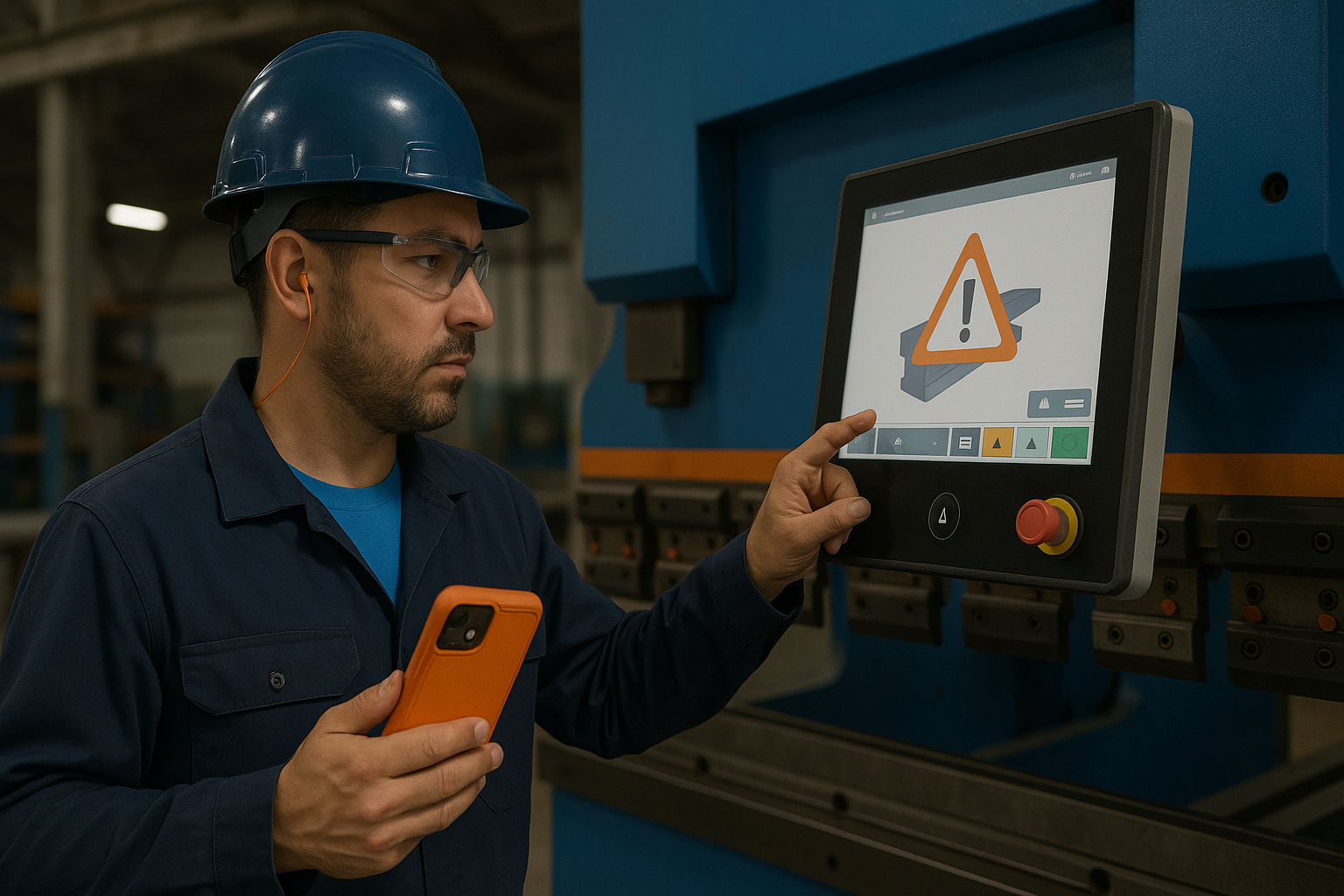
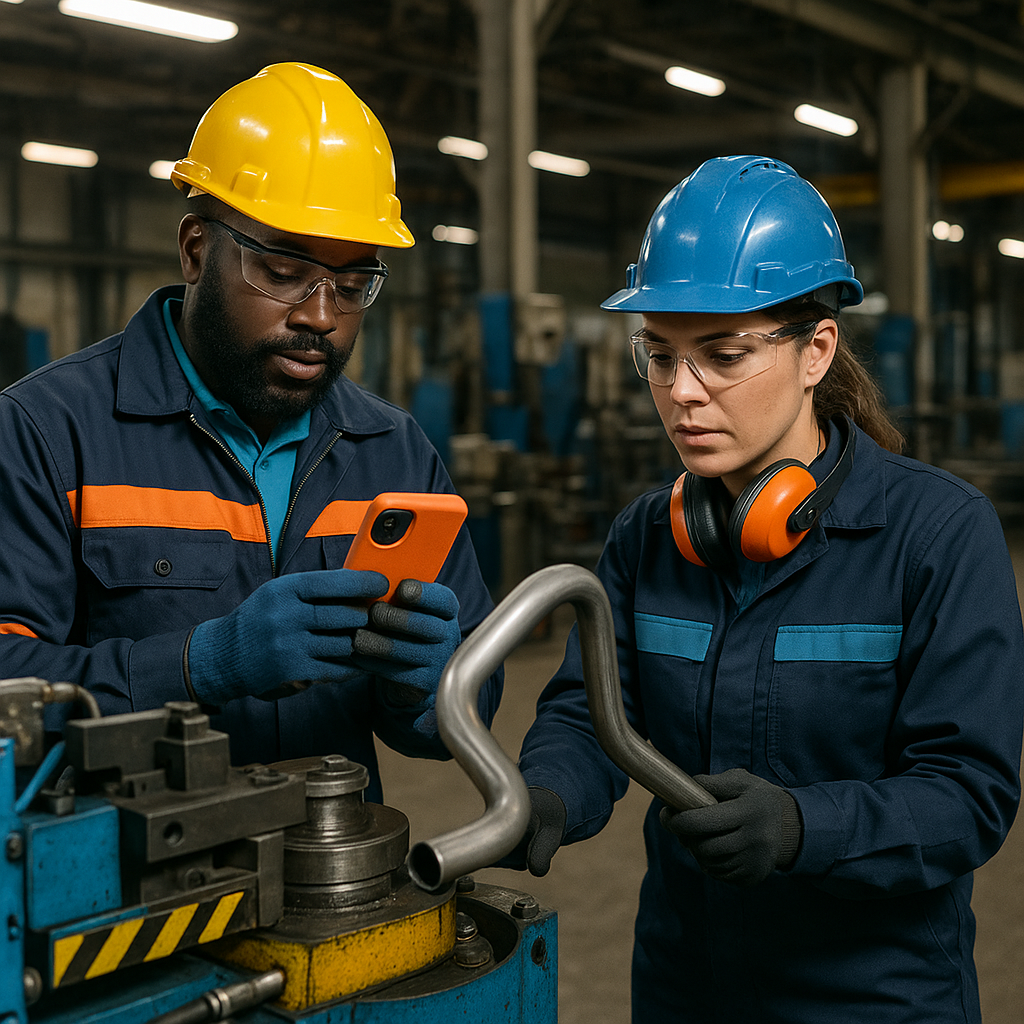
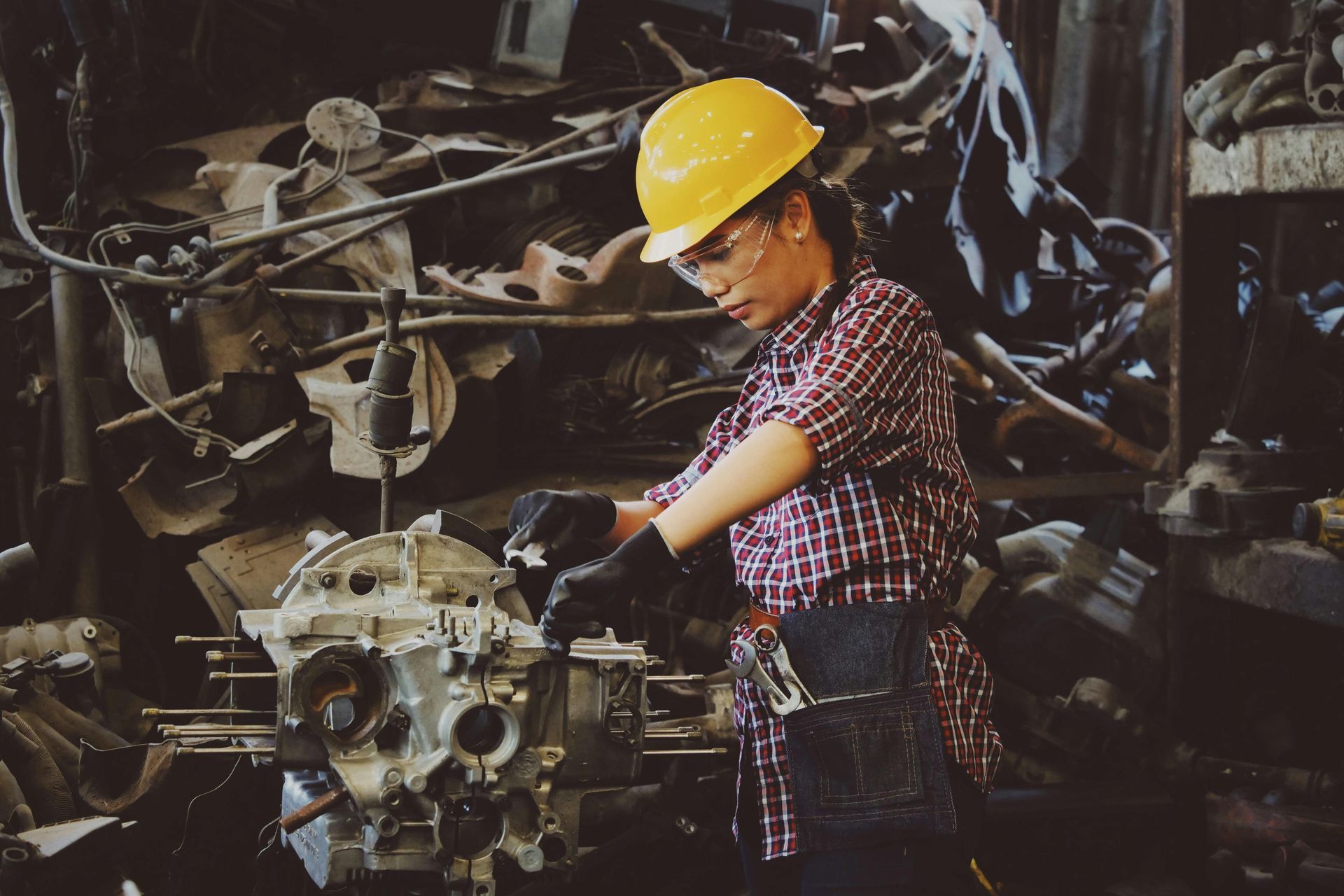
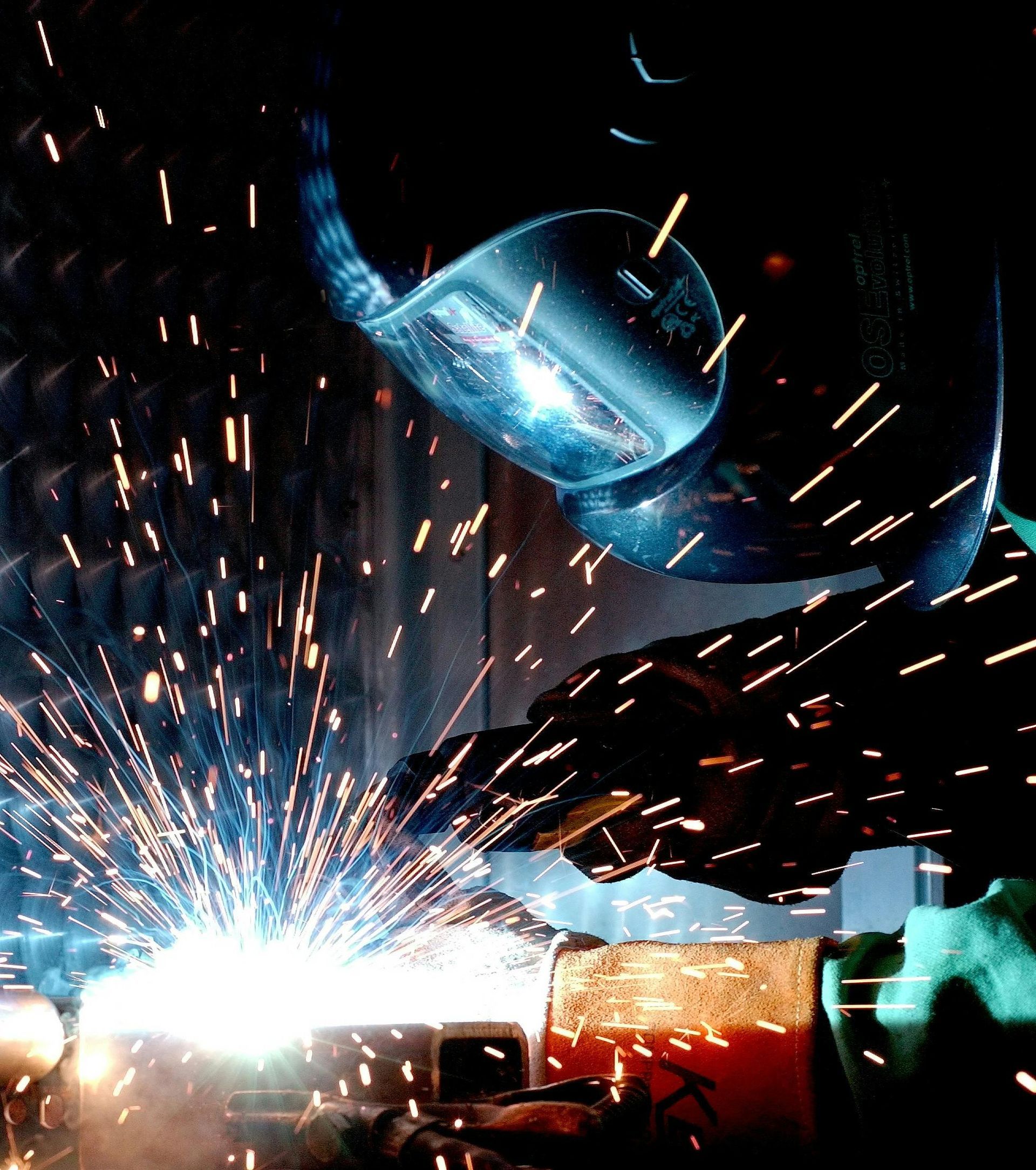