Connected Worker Blog
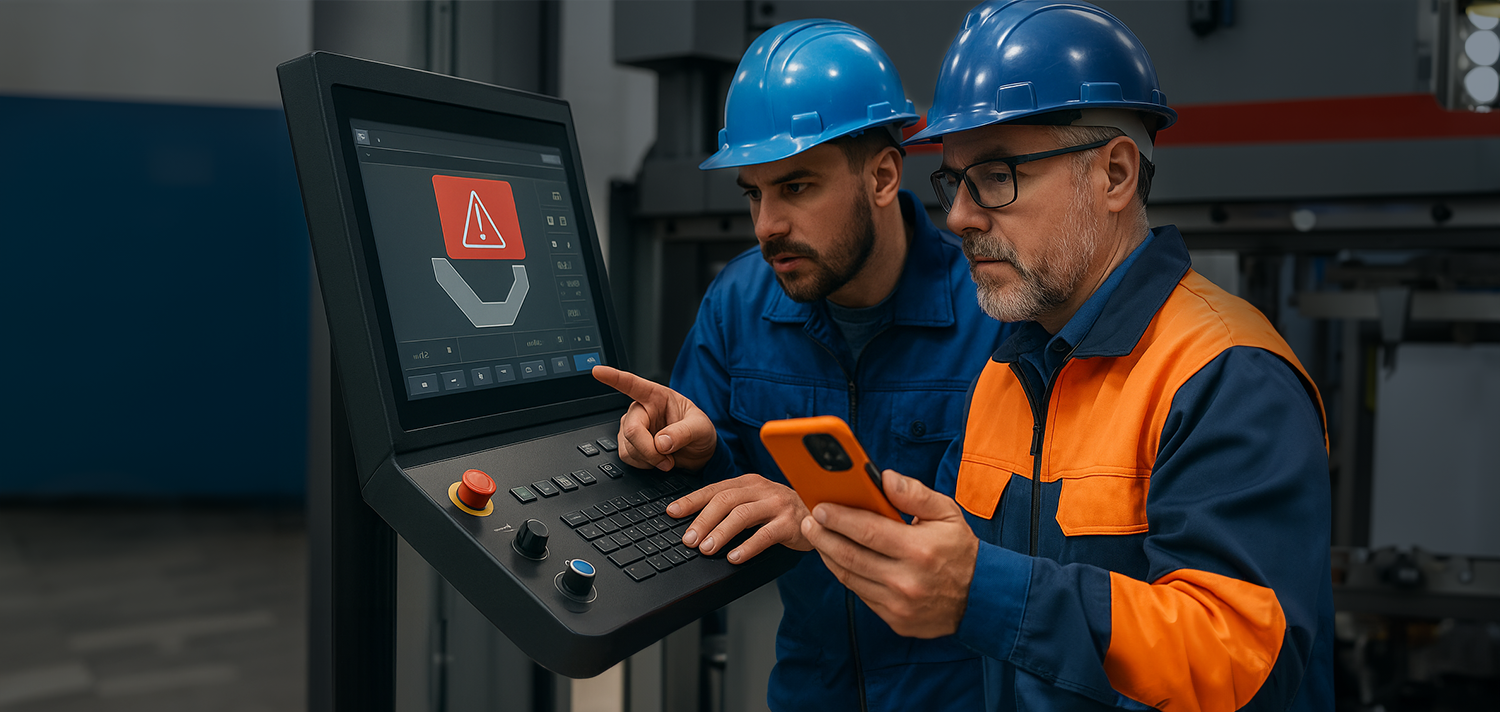
Whether you’re managing metal manufacturing processes or optimizing operational efficiency, Planned Maintenance (PM) is a critical pillar of Total Productive Maintenance (TPM) that helps prevent unexpected equipment failures . By implementing PM strategies, manufacturers can reduce unplanned downtime, lower maintenance and repair costs, and improve overall productivity . The Cost of Unplanned Downtime in Metal Manufacturing Unplanned downtime is one of the most significant challenges in the metal manufacturing industry. It: Disrupts production schedules Increases repair costs Impacts overall profitability By implementing Planned Maintenance (PM) and scheduling regular inspections and preventive maintenance tasks , PM helps manufacturers address potential issues before they escalate into costly breakdowns. What Is Planned Maintenance? Planned Maintenance (PM) involves creating a schedule for: Routine equipment care based on historical data Usage patterns Condition monitoring This proactive approach ensures that maintenance tasks are performed at optimal intervals , reducing the likelihood of unexpected failures. Key Benefits of Planned Maintenance Reduced Unplanned Downtime: PM minimizes disruptions by addressing issues proactively Lower Maintenance Costs: Preventive care is significantly less expensive than emergency repairs Extended Equipment Lifespan: Regular upkeep prevents wear and tear, maximizing asset longevity Improved Operational Efficiency: Reliable equipment ensures smoother production processes Real-Life Example: Aluminum Fabricator in Nashville At a large aluminum fabrication plant in Nashville, Tennessee, a press brake operator demonstrated the power of Planned Maintenance : During daily checks, he noticed a gradual drop in hydraulic pressure through sensor alerts The operator promptly reported the issue to the maintenance team The maintenance team replaced a worn-out press seal before it failed completely This proactive intervention prevented an unplanned breakdown during a high-demand production period. As a result: Press brake downtime was reduced by 50% Overall Equipment Effectiveness (OEE) improved from 70% to 76% This example highlights how trained operators can play a pivotal role in reducing downtime and improving efficiency through PM practices Impact of Planned Maintenance on Costs and Productivity Planned maintenance is focuses on using regular checks and data to plan maintenance in advance , making sure equipment stays reliable and available while keeping costs low. The effective adoption of PM brings measurable benefits: including increased OEE by reducing unexpected failures and downtime , as well as lower maintenance costs with fewer emergency interventions. It also contributes to extending the useful life of equipment , improving operational safety, and stabilizing operating conditions, resulting in higher product quality . (Kaizen Institute) Why PM Is Essential for Metal Manufacturers Operations leaders in metal manufacturing are increasingly recognizing the value of Planned Maintenance as part of their TPM strategy. By proactively addressing potential issues, PM not only reduces unplanned downtime but also controls high maintenance costs and extends equipment lifespan. Learn More For more insights into TPM strategies and how Planned Maintenance supports operational efficiency, visit TPM impact on Metal Manufacturing . And that’s your Corvex Connected Workforce Quick Take!
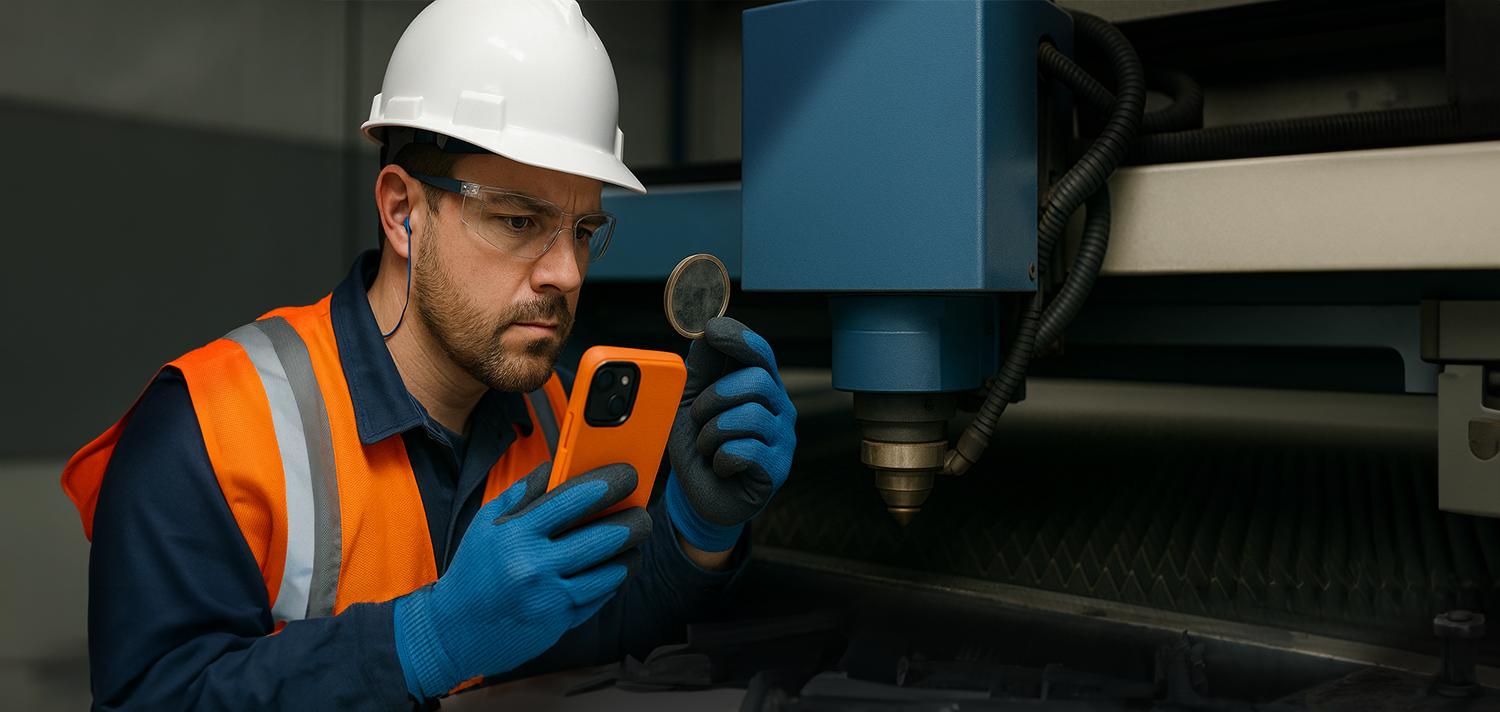
Whether you’re overseeing production lines or ensuring quality in manufacturing, Planned Maintenance (PM) is a vital part of Total Productive Maintenance (TPM) that keeps everything on track. By adopting PM strategies, manufacturers can: Directly address quality control challenges Reduce defects and enhance product consistency Minimize costly rework. The Cost of Production Bottlenecks in Metal Manufacturing Production bottlenecks are a nightmare for metal manufacturers. They disrupt workflows, delay orders, and increase operational costs. Unplanned downtime caused by equipment failures can lead to significant production delays and financial losses. Planned Maintenance (PM) offers a solution by focusing on preventive care to keep machines running smoothly. PM involves scheduling regular maintenance tasks—such as cleaning, inspections, and minor repairs—to catch small issues before they escalate into major problems. What Is Planned Maintenance? Planned Maintenance (PM) is a systematic approach to maintaining equipment through routine checks and preventive actions. Unlike reactive maintenance, which addresses issues after they occur, PM is proactive and ensures equipment reliability. Key Benefits of Planned Maintenance Avoiding Bottlenecks: PM reduces the risk of unexpected breakdowns that disrupt production Boosting Productivity: Reliable equipment ensures consistent throughput Lowering Costs: Preventive care minimizes expensive emergency repairs Improving Safety: Well-maintained machines reduce workplace hazards Real-Life Example: Plumbing Products Fabrication Plant in Michigan At a commercial plumbing products fabrication plant in Michigan, a laser cutter operator noticed reduced cutting precision during routine Planned Maintenance checks. Here’s what happened: The operator identified dirty optics and a clogged air filter as the root causes Using her TPM training, she cleaned the optics and replaced the filter This quick intervention restored the machine’s full functionality without requiring maintenance team involvement The result? The plant avoided a production bottleneck during a high-demand sink order, saving an estimated $10,000 in lost production costs and ensuring on-time delivery. Impact of Planned Maintenance on Avoiding Unplanned Disruptions Planned maintenance involves implementing two main types of actions: preventive and post-failure. These actions play a key role in ensuring equipment availability and reliability, minimizing unplanned downtime, and improving operational efficiency. (Kaizen Institute) By addressing potential issues before they lead to breakdowns, maintenance can be performed during scheduled windows rather than emergency situations. This approach stabilizes operations and boosts both productivity and equipment reliability. Avoiding Disruptions with Planned Maintenance For metal manufacturers, Planned Maintenance is more than just a strategy—it’s a necessity for avoiding bottlenecks and keeping operations on track. By addressing small issues early, PM ensures smoother workflows, improved reliability, and greater cost savings. Learn More For more insights into TPM strategies and how Planned Maintenance supports operational efficiency, visit TPM impact on Metal Manufacturing And that’s your Corvex Connected Workforce Quick Take!
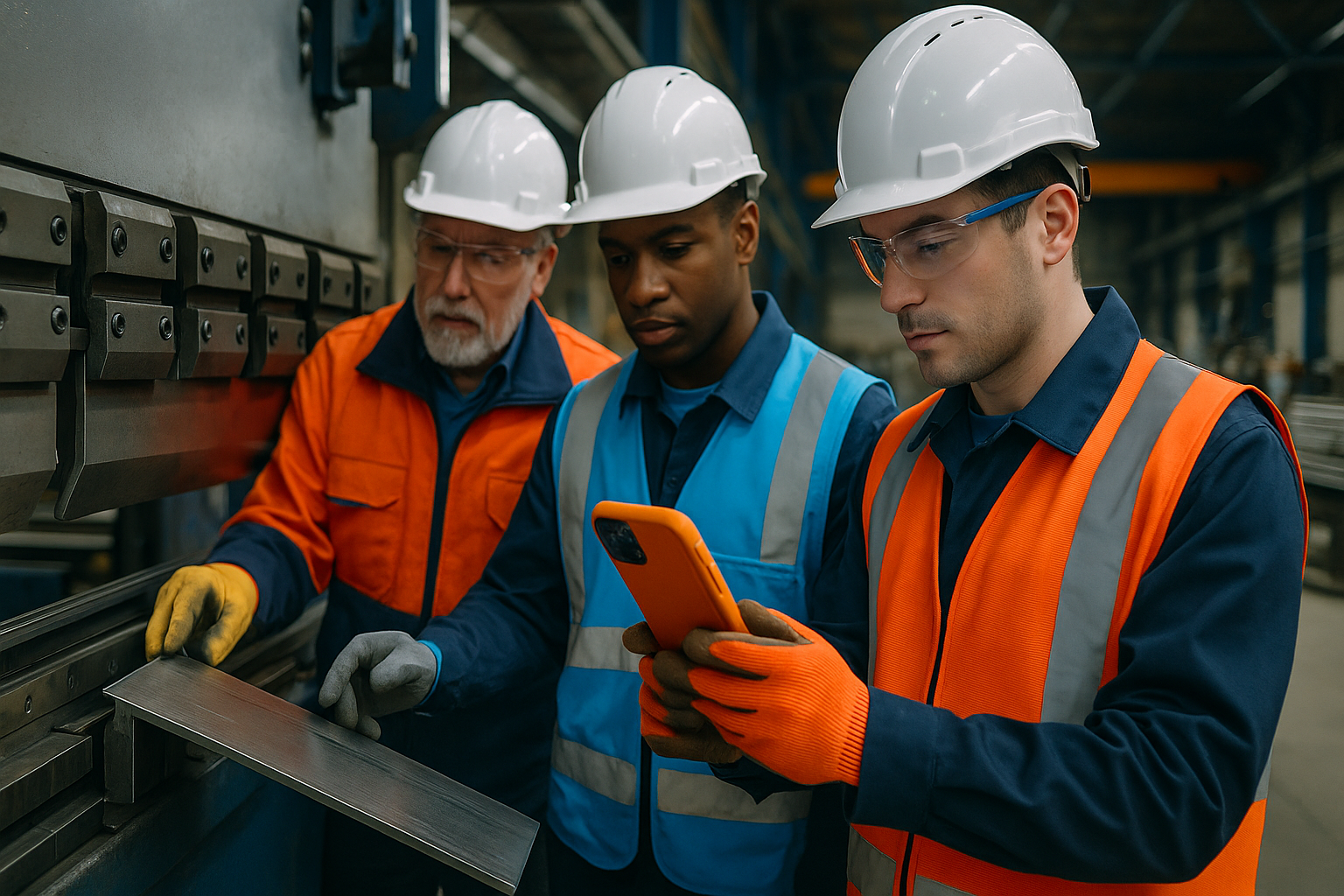
Whether you're operating stamping presses, laser cutters, or robotic welding cells, equipment reliability is essential in metal manufacturing environments. The following overview of Total Productive Maintenance (TPM) will provide insights to help eliminate unplanned downtime , reduce defects, and empower operators to take ownership of equipment care—all while fostering a safer, more efficient workplace. What is Total Productive Maintenance (TPM)? Total Productive Maintenance (TPM) is a comprehensive approach to equipment maintenance designed to achieve “perfect production.” Unlike traditional reactive maintenance, TPM emphasizes proactive and preventive care by involving everyone on the factory floor—especially machine operators—in maintaining equipment health. By breaking down the barriers between production and maintenance, TPM creates a culture of shared responsibility and continuous improvement, ultimately maximizing operational efficiency. Key TPM Goals Zero Breakdowns: TPM proactively prevents unexpected equipment failures that cause production stoppages Increased Equipment Effectiveness: Regular maintenance ensures machines run smoothly without minor interruptions that reduce efficiency Enhanced Safety: TPM fosters a safer work environment by addressing potential hazards before accidents occur Operator Empowerment: Training and involving operators in maintenance creates ownership and quicker problem detection Continuous Improvement: TPM encourages ongoing refinement of processes to boost productivity and reliability How TPM Helps in Metal Manufacturing Facilities In metal manufacturing, unplanned downtime and defects can disrupt production and increase costs. TPM tackles these issues by involving operators in regular equipment care , preventing breakdowns before they happen. This collaborative approach: Boosts machine reliability Improves product quality Enhances workplace safety This are the key factors for efficient and competitive metal manufacturing operations. The 8 TPM pillars: What They Are and How They Improve Your Production Total Productive Maintenance is built on eight foundational pillars that guide how organizations approach equipment care and operational excellence. Understanding and applying these pillars to your daily tasks helps build a culture of continuous improvement and shared responsibility across your entire facility. To make it easy to consume, we’ve put together an infographic to help you visualize these pillars and see how they can be applied effectively in your maintenance and production processes.
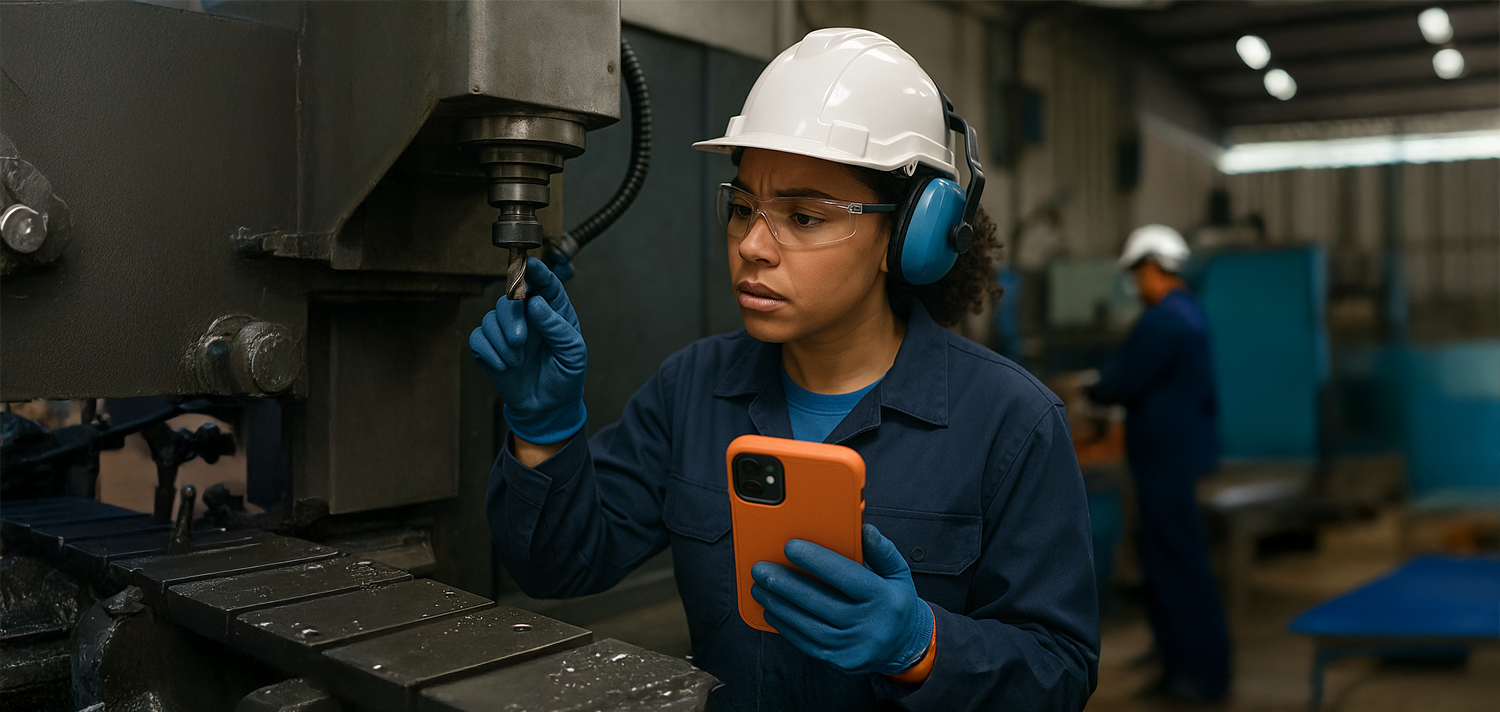
Whether you’re overseeing production lines or ensuring quality in manufacturing, Planned Maintenance (PM) is a vital part of Total Productive Maintenance (TPM) that keeps everything on track. By adopting PM strategies, manufacturers can directly address quality control challenges, reduce defects, enhance product consistency, and minimize costly rework. Why Quality Control Matters in Metal Manufacturing In metal manufacturing, even minor quality control issues can lead to significant problems like production delays, customer dissatisfaction, and increased costs. Implementing robust quality control measures helps in identifying and rectifying defects early in the production process. Planned Maintenance (PM) plays a crucial role in maintaining high-quality standards by ensuring that equipment functions optimally. Regular maintenance tasks like cleaning, calibrating, and inspecting equipment prevent defects from occurring in the first place. The Role of Planned Maintenance in Quality Control Planned Maintenance (PM) is a proactive approach that helps manufacturers maintain consistent product quality by addressing equipment issues before they escalate. It involves scheduling routine inspections and preventive tasks to ensure machines operate at peak performance. Key Benefits of Planned Maintenance for Quality Control Reduced Defects: PM minimizes equipment-related errors that lead to defective products Improved Consistency: Well-maintained machines produce uniform products, meeting customer specifications every time Lower Rework Costs: Preventing defects reduces the need for rework and associated expenses Real-Life Example: Machining Plant in North Carolina At a machining plant in North Carolina that produces precision aerospace and medical components, a CNC milling machine operator noticed slight dimensional inaccuracies during routine Planned Maintenance checks. Here’s what happened: The operator identified worn cutting tools as the root cause Using her TPM training, she replaced the tools immediately This quick intervention prevented further inaccuracies in machined parts The result? The plant reduced rework by 30% and ensured consistent quality in high-precision components critical for aerospace and medical applications Impact of Planned Maintenance on quality According to the Kaizen Institute , planned maintenance reduces the occurrence of quality defects and rework. Organizations can gain a significant competitive advantage in the market by implementing planned maintenance strategies. Additionally, properly calibrated and precisely aligned machines ensure continuous productivity, resulting in higher-quality outputs with less material loss. Managing Quality with Planned Maintenance For metal manufacturers, Planned Maintenance is more than just a maintenance strategy—it’s a critical tool for managing quality control issues. By proactively addressing equipment problems, PM helps reduce defects, improve product consistency, and boost overall productivity. Learn More For more insights into TPM strategies and how Planned Maintenance supports quality, visit Lean Production’s TPM Framework And that’s your Corvex Connected Workforce Quick Take!
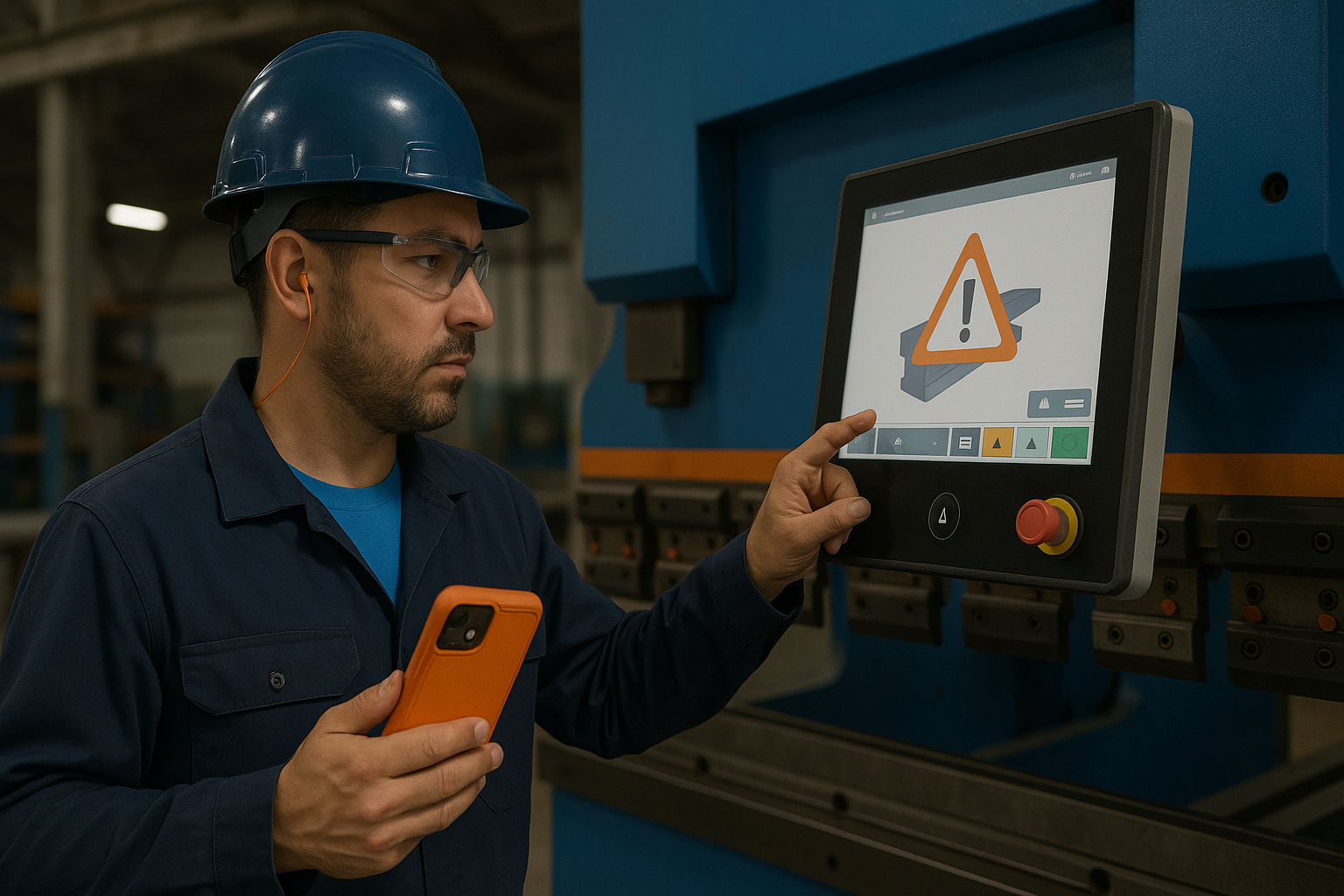
Whether you're managing CNC machines on the factory floor or coordinating teams in heavy metal manufacturing, Planned Maintenance (PM) is a critical practice that keeps operations running smoothly. As a key pillar of Total Productive Maintenance (TPM), PM helps reduce unplanned downtime, extend equipment life, and control costs. The Challenge of Unplanned Downtime Unplanned downtime is one of the most significant challenges faced by metal manufacturers. Equipment failures not only disrupt production schedules but also lead to costly repairs and lost revenue. lubrication, inspections, and minor repairs. Unplanned downtime costs industrial manufacturers an estimated $50 billion annually (WSJ/Emerson) . This is where Planned Maintenance (PM) comes into play. PM involves scheduling regular inspections, preventive maintenance tasks, and repairs to address issues before they escalate. It’s a proactive approach that ensures equipment operates reliably and efficiently. The Role of Planned Maintenance in TPM Planned Maintenance (PM) is one of the eight pillars of Total Productive Maintenance (TPM). TPM is a manufacturing strategy designed to optimize equipment reliability, minimize downtime, and enhance product quality. PM focuses on scheduling maintenance activities systematically to prevent unexpected breakdowns. Key Benefits of Planned Maintenance Reduced Unplanned Downtime: Regular inspections help identify issues early Improved Equipment Lifespan: Preventive care extends asset life Enhanced Productivity: Reliable machines keep production lines running smoothly Lower Maintenance Costs: Proactive repairs cost significantly less than emergency fixes Real-Life Example: Aluminum Fabricator in Nashville At a large aluminum fabrication plant in Nashville, Tennessee, a press brake operator implemented Planned Maintenance principles during daily checks: The operator noticed a gradual drop in hydraulic pressure through sensor alerts Reported the issue to the maintenance team The team replaced a worn-out press seal before it failed completely This proactive intervention prevented an unplanned breakdown during a high-demand production period, reducing downtime for the press brake by 50% while improving overall equipment efficiency (OEE) from 70% to 76%. This demonstrates how trained operators can contribute directly to productivity and cost savings. Benefits of Planned Maintenance The impact of Planned Maintenance extends beyond individual success stories. According to a report by McKinsey , operations implementing PM experienced: 30% Maintenance Cost Savings Up to 50% reduction of Unplanned Downtime Additionally, reactive maintenance can cost three to four times more than preventive and planned maintenance (Powerhouse Dynamics) . Maximizing Uptime with Planned Maintenance Operations leaders across the metal manufacturing industry are increasingly adopting Planned Maintenance strategies as part of their TPM programs. By proactively addressing equipment issues before they escalate, manufacturers can achieve: Reduced downtime Improved reliability Enhanced safety Lower costs Learn More For more insights into TPM strategies and how Planned Maintenance supports operational excellence, visit Lean Production’s TPM Framework And that’s your Corvex Connected Workforce Quick Take!
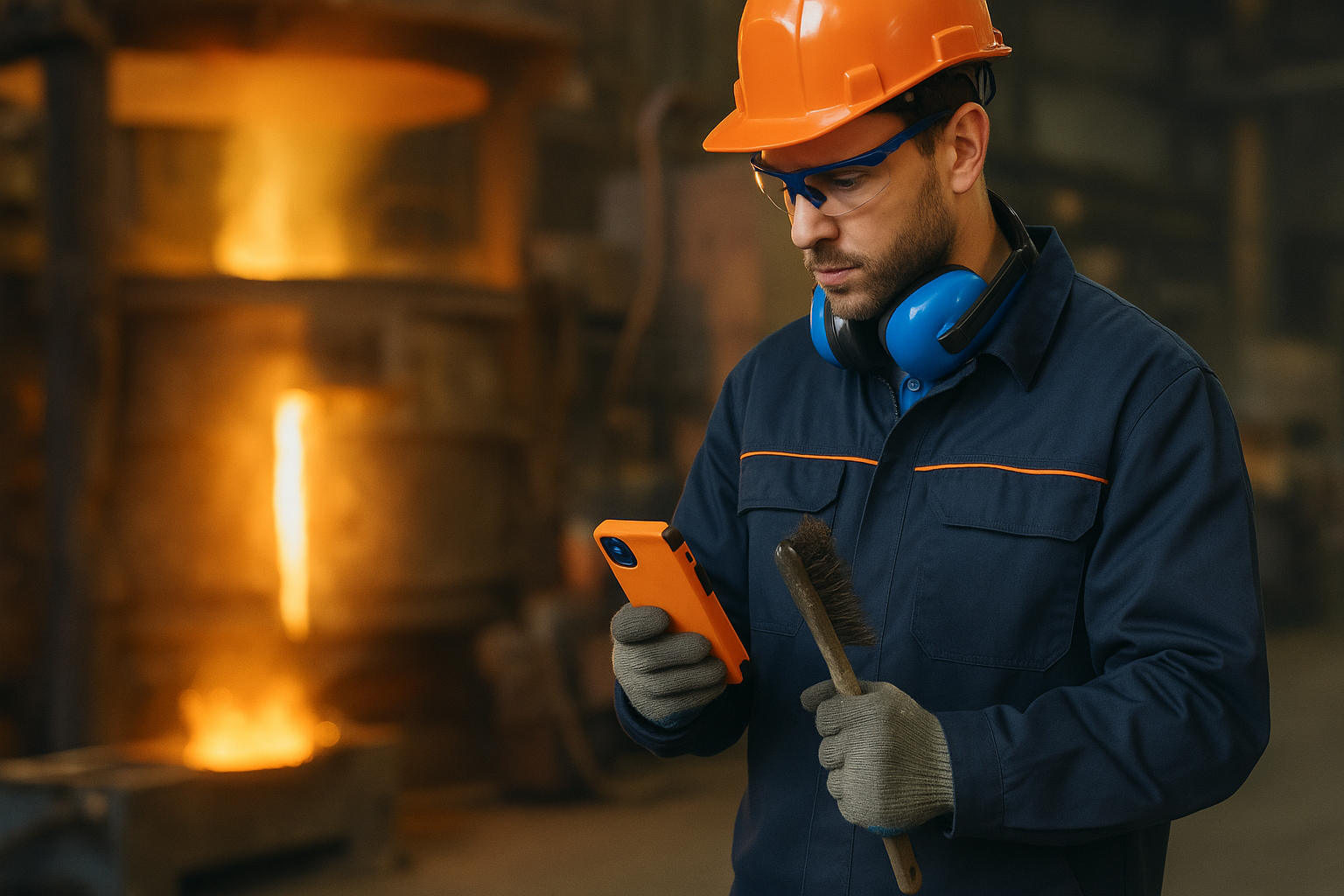
The Foundations of Autonomous Maintenance and Planned Maintenance Autonomous Maintenance (AM) empowers operators to take ownership of routine equipment care, such as cleaning, lubrication, and minor repairs. This proactive approach fosters a culture of accountability, reduces downtime, and extends equipment lifespan. On the other hand, Planned Maintenance (PM) involves scheduled interventions by maintenance teams to prevent breakdowns and address wear and tear through inspections, repairs, and replacements. Key Benefits of Autonomous Maintenance: Reduced Downtime: Operators identify potential issues early, preventing unplanned stoppages Improved Equipment Lifespan: R outine care prevents excessive wear Enhanced Operator Productivity: Empowered operators take pride in their role Key Benefits of Autonomous Maintenance: Proactive Problem Prevention: Scheduled downtime avoids costly disruptions Focus on Complex Repairs: Dedicated teams handle advanced maintenance tasks How AM and PM Work Together in TPM While AM focuses on empowering operators for daily care tasks, PM ensures that deeper issues are addressed systematically. Together, these strategies create a balanced approach to equipment reliability and operational efficiency. Operators learn to identify emerging issues before they escalate. R eal-Life Success Story: Casting Plant in Milwaukee At a casting plant in Milwaukee, Wisconsin, a CNC machining operator trained in Autonomous Maintenance noticed coolant levels dropping during routine checks. Following AM principles: The operator inspected the machine independently Identified a leaking hose Replaced the hose and cleaned the area thoroughly This proactive effort prevented a coolant spill that could have created slip hazards and ensured uninterrupted machine operation without external intervention. By combining AM with PM strategies, the plant achieved safer operations and improved productivity. The Transformative Impact of Autonomous Maintenance and Planned Maintenance According to the Kaizen Institute A M results in greater equipment reliability, reduction of failures, increased lifespan, reduced downtime, and overall improvement in operational performance. Planned maintenance aims to maximize equipment availability through efficient planning of maintenance activities . When combined—AM empowering operators to detect early issues and PM ensuring systematic upkeep—these strategies yield powerful synergies that significantly enhance equipment reliability, reduce disruptions, and elevate productivity. Drive Excellence with TPM Leaders in casting operations are increasingly turning to TPM initiatives like Autonomous Maintenance to enhance safety, reliability, and productivity. By empowering operators through AM and complementing it with PM strategies, metal manufacturing plants can unlock unparalleled efficiency and resilience. Learn More For more insights into TPM strategies and their benefits, visit Lean Production’s TPM Framework And that’s your Corvex Connected Workforce Quick Take!
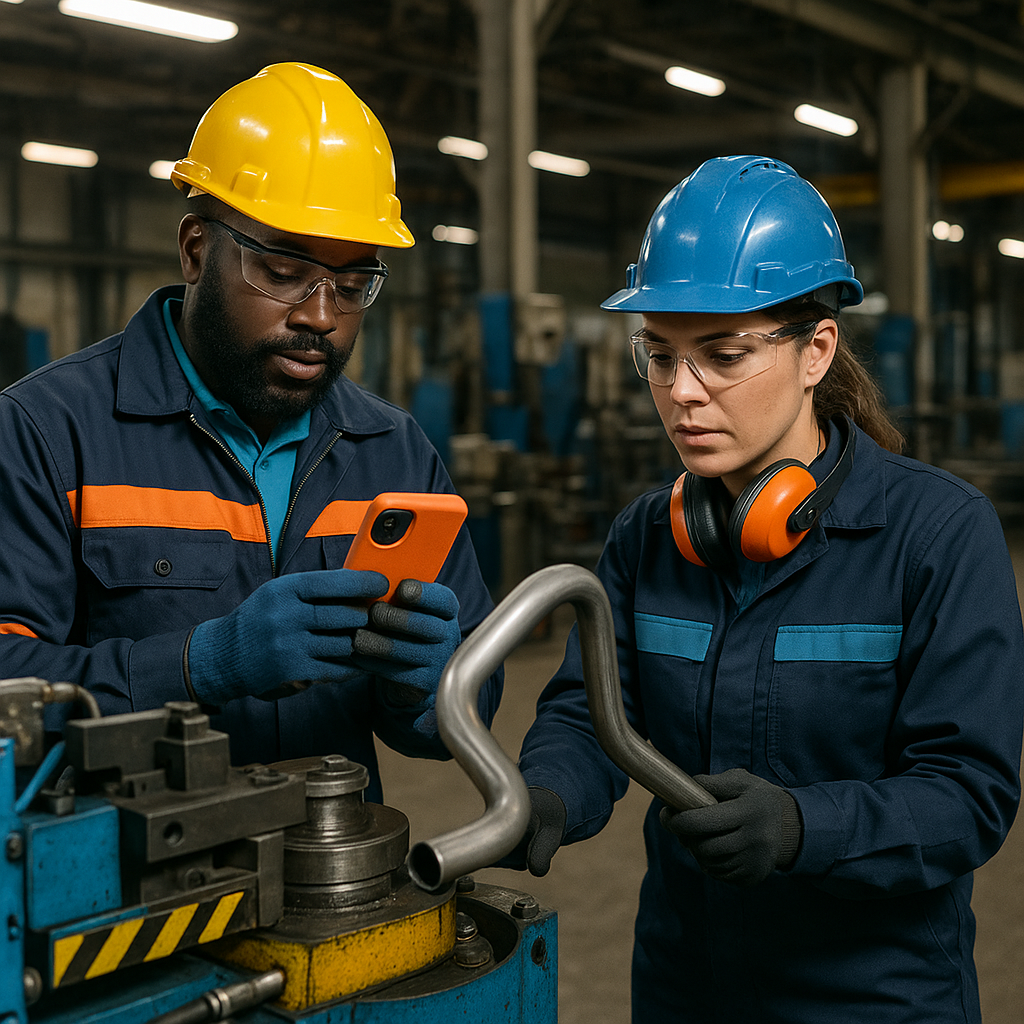
Whether you're managing high-capacity press brakes or automated tube bending machines, workplace safety is paramount in metal manufacturing environments, the following Autonomous Maintenance (AM) guidance will provide insights to enhance workplace safety , reduce hazards, and empower operators to take ownership of equipment care. Why Safety Matters in Metal Manufacturing Metal manufacturing facilities, such as pipe and tube plants serving construction and energy industries, face unique challenges related to workplace safety. Heavy machinery, high temperatures, and complex equipment create risks that require proactive strategies to mitigate. This is where Autonomous Maintenance (AM) comes into play. Key Benefits of Autonomous Maintenance for Safety: Proactive Hazard Prevention: Operators identify and address issues before they escalate. Improved Equipment Reliability: Routine upkeep minimizes unexpected failures that could lead to accidents Enhanced Operator confidence: Empowered operators take ownership of safety The Role of AM in Total Productive Maintenance (TPM) Autonomous Maintenance (AM) is one of the eight pillars of Total Productive Maintenance (TPM). It focuses on empowering operators to perform routine maintenance tasks such as cleaning, inspections, and minor repairs. By fostering a culture of shared responsibility between operators and maintenance teams, AM ensures that equipment operates safely and efficiently. How AM Improves Safety: Early Problem Detection: Operators spot issues like leaks or wear during routine checks. Consistent Equipment Care: Regular cleaning and lubrication prevent deterioration. Structured Training: Operators gain the skills needed to maintain equipment safely Real-Life Example: Pipe and Tube Plant in Bethlehem At a pipe and tube manufacturing plant in Bethlehem, Pennsylvania, an operator noticed unusual vibrations during routine Autonomous Maintenance checks on a tube bending machine. Here’s how AM principles prevented a potential hazard: The operator inspected the hydraulic system and discovered a loose fitting causing fluid leakage—a potential slip hazard. Tightened the fitting and cleaned the area thoroughly. Checked the machine’s safety guards for proper alignment. These proactive actions not only prevented a workplace accident but also avoided damage to critical components that could have led to downtime. By empowering operators through AM training, the plant ensured safer operations and uninterrupted production schedules. The Impact of AM on Workplace Safety According to the Kaizen institute "AM contributes to creating a safer work environment. Operators involved in maintenance activities become more aware of the risks and necessary safety measures. This results in a reduction in accidents and equipment-related injuries." Driving Safety with TPM Operations leaders across the metal manufacturing industry are increasingly adopting technologies that support TPM initiatives like Autonomous Maintenance. By empowering operators to take ownership of routine maintenance tasks, manufacturers can reduce workplace hazards, improve reliability, and boost productivity. Learn More For more insights into TPM strategies and their benefits for workplace safety, visit: SafetyCulture’s Guide to Total Productive Maintenance Camcode’s Overview of Autonomous Maintenance MaintainX’s Beginner’s Guide to Autonomous Maintenance And that’s your Corvex Connected Workforce Quick Take!
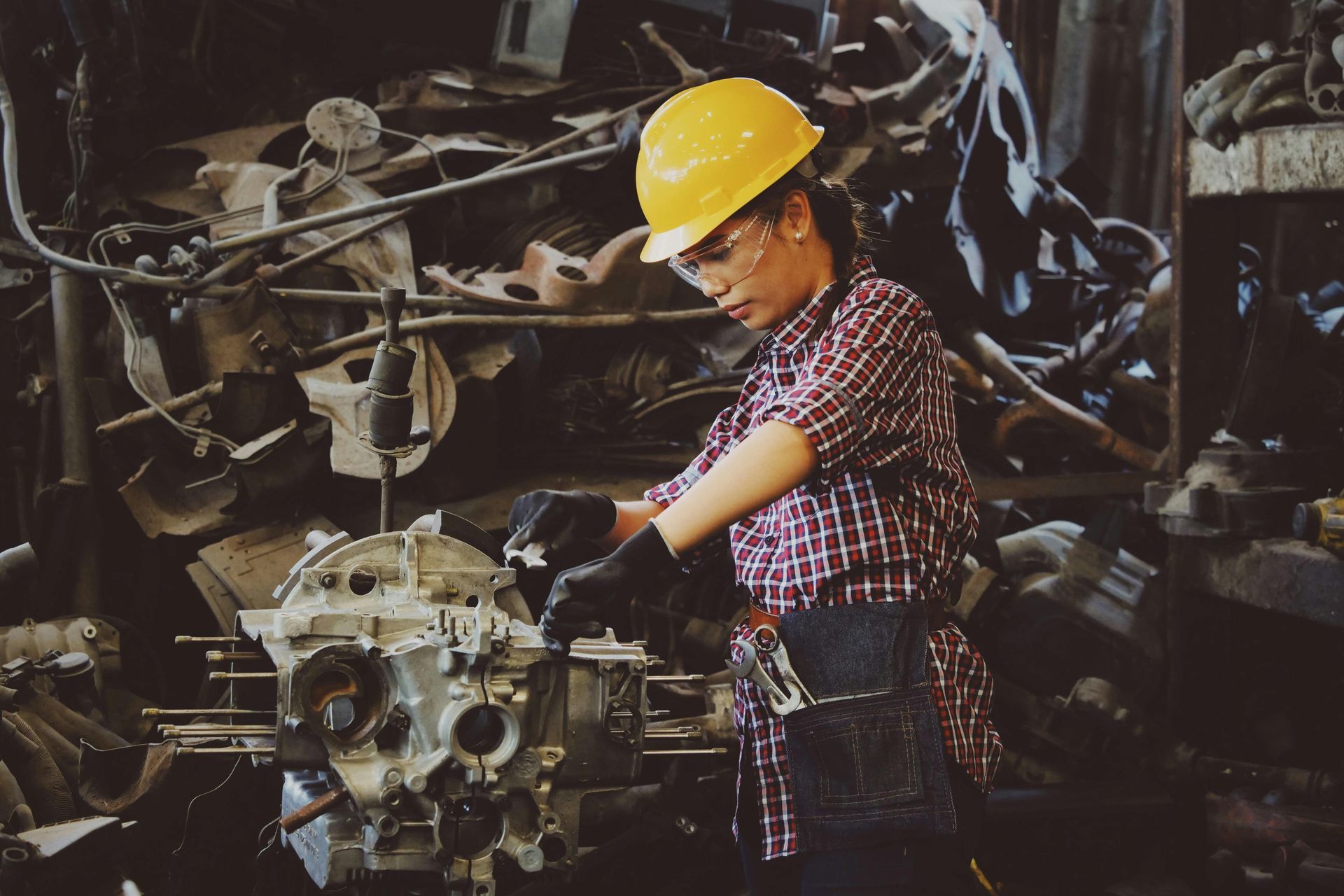
Why Training Is Essential for Autonomous Maintenance Proper training empowers operators to take ownership of equipment care, driving efficiency, safety, and reliability in manufacturing environments. Autonomous Maintenance (AM) equips operators with the skills needed to perform routine maintenance tasks such as cleaning, lubrication, inspections, and minor repairs. However, without proper training, operators may lack the confidence and technical knowledge required to identify issues or perform preventive tasks effectively. Key Benefits of Training for AM Improved Equipment Reliability: Operators learn to detect abnormalities early, preventing breakdowns Enhanced Operator Confidence: Training instills a sense of ownership and responsibility Increased Efficiency: Plants implementing AM training see up to a 10–15% boost in overall efficiency How Training Fits into Total Productive Maintenance (TPM) Training is one of the foundational elements of TPM and is essential for successful implementation of AM. It ensures operators understand their equipment deeply—its components, common issues, and troubleshooting procedures. This knowledge enables them to perform routine maintenance tasks confidently and proactively. Key Skills Developed Through Training 1. Problem Detection: Operators learn to identify emerging issues before they escalate. 2. Technical Knowledge: Comprehensive understanding of machine components and their functions. 3. Maintenance Procedures: Proper cleaning, lubrication, and calibration techniques Real-Life Example: Fabricated Plate Work Plant in Mobile At a fabricated plate work plant in Mobile, Alabama, a plasma cutter operator noticed inconsistent cutting precision during routine AM checks. Here’s how targeted training helped resolve the issue: The operator identified worn consumables causing the problem She replaced the cutting nozzle and cleaned guide rails to remove debris buildup She recalibrated the system to restore cutting accuracy Then she documented findings with photos and shared feedback with the maintenance team to refine inspection protocols These actions prevented production delays and eliminated potential safety hazards like overheating caused by worn components. The Transformative Impact of Autonomous Maintenance Training Investing in operator training is not just an expense—it’s a necessity for effective AM programs. According to the Society for Maintenance and Reliability Professionals ( SMRP ): Facilities implementing AM training programs experience up to a 40% increase in asset lifespan Operators gain confidence, reducing reliance on reactive maintenance Additionally, structured training programs foster a culture of continuous learning and improvement, ensuring operators stay updated with emerging technologies and best practices. Closing Thoughts: Driving Excellence Through Training Leaders in metal manufacturing understand that training is the cornerstone of successful Autonomous Maintenance programs. By equipping operators with the skills needed to maintain their equipment proactively, manufacturers can reduce downtime, improve reliability, and enhance workplace safety. Learn More For more insights into TPM strategies and their benefits, visit Lean Production’s TPM Framework And that’s your Corvex Connected Workforce Quick Take!
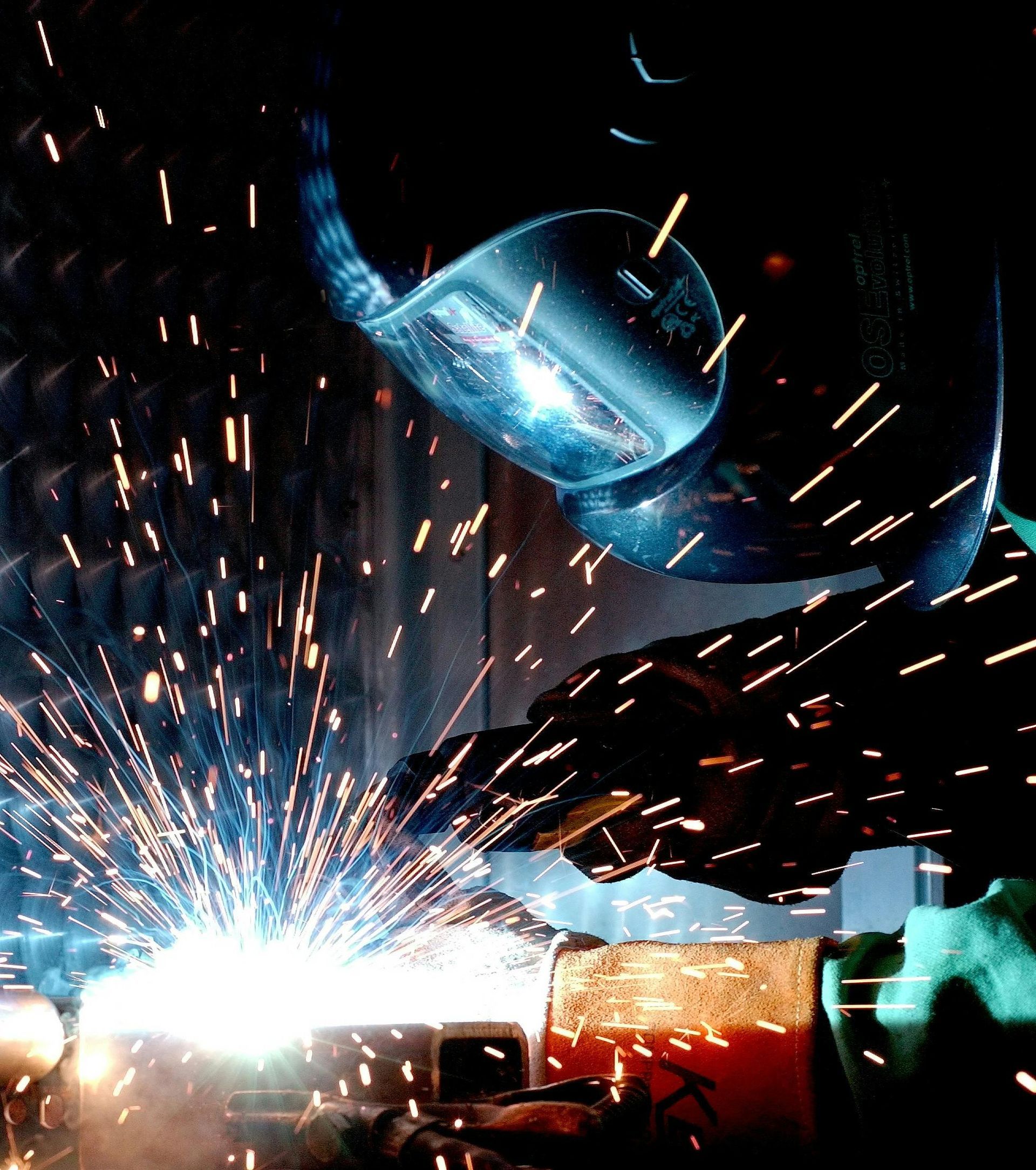
Whether you’re operating waterjet cutters in aerospace manufacturing or CNC machining centers in metalworking, the following Autonomous Maintenance guidance will provide actionable insights to transform your operations. The Role of Autonomous Maintenance in Equipment Reliability Autonomous Maintenance (AM) empowers operators to take ownership of routine maintenance tasks, such as cleaning, lubrication, and inspections. By decentralizing these activities, AM fosters a culture of accountability and early problem detection, ensuring that equipment operates at peak performance. This proactive approach reduces reliance on reactive maintenance and helps prevent costly breakdowns. Key Benefits of Autonomous Maintenance: Reduced Downtime: Operators identify issues early, preventing unplanned stoppages Improved Equipment Lifespan: Routine care prevents excessive wear and damage Enhanced Safety: Proactive maintenance reduces risks associated with equipment failures While Autonomous Maintenance (AM) focuses on empowering operators to perform daily care tasks, Planned Maintenance (PM) involves scheduled interventions by maintenance teams based on equipment condition and usage data. Together, these pillars of TPM create a balanced approach to reliability and efficiency. Key Differences Autonomous Maintenance: Daily tasks like cleaning, inspections, and minor repairs performed by operators Planned Maintenance: Scheduled activities like part replacements and major repairs handled by maintenance teams Real-Life Example: Aerospace Manufacturer in Spokane At an aerospace manufacturing facility in Spokane, Washington, a waterjet operator implemented Autonomous Maintenance principles to address irregular pressure levels during routine checks. Here’s how the process unfolded: Cleaning Abrasive Feed Lines: This prevented blockages that could have disrupted precision cutting Inspecting Seals for Wear: This ensured optimal machine performance Replacing a Worn Nozzle: This maintained cutting accuracy; critical for aerospace-grade components Documenting Findings: Photos were taken to streamline future inspections and improve nozzle replacement procedures These actions not only maintained cutting precision but also prevented downtime that could have disrupted production schedules The Transformative Impact of Autonomous Maintenance Operations leaders in industries like aerospace and metal manufacturing are increasingly adopting AM initiatives due to their profound impact on reliability and productivity. According to the Kaizen Institute : Facilities implementing AM see up to a 40% reduction in equipment downtime Equipment lifespan increases by up to 50%, significantly lowering long-term costs Moreover, AM fosters employee engagement by empowering operators with the skills and responsibility to maintain their machines effectively. This leads to higher morale, improved safety standards, and enhanced operational efficiency. Driving Excellence with TPM Autonomous Maintenance is not just about reducing downtime—it’s about transforming how manufacturers approach equipment care. By integrating AM into your TPM strategy, you can unlock new levels of reliability, safety, and productivity while fostering a culture of continuous improvement. Learn More For more insights into TPM strategies and their benefits, visit Lean Production’s TPM Framework And that’s your Corvex Connected Workforce Quick Take!