What are the 7 Steps of Autonomous Maintenance?
Here at Corvex, we've had many discussions with leaders in welding operations about how Autonomous Maintenance empowers operators to keep their robotic systems running efficiently and safely.
Welding operations, especially those using robotic MIG and TIG welders, rely on precision and consistency to meet production demands.
Autonomous Maintenance equips and enables operators to maximize productivity. They not only manage routine upkeep, ensuring smooth operations, but they also reduce reliance on reactive maintenance.
Question
Are you familiar with the seven steps of Autonomous Maintenance, and how they can be implemented to benefit welding operations?
Answer
Autonomous Maintenance is a structured process that empowers operators to perform basic care tasks, keeping equipment in top condition. It follows seven key steps.
Step 1 - Increase Operator Knowledge
Operators become the heartbeat of robotic welding, mastering every detail—from the precision of sensors to the movement of nozzles and arms. They don’t just run the machines; they understand them.
A study in Manaus, Brazil, found that implementing Autonomous Maintenance boosted operator knowledge by 39%, empowering them to catch issues before they escalate. This isn’t just about efficiency—it’s about ownership, pride, and ensuring every weld meets the highest standard.
Step 2 - Initial Cleaning and Inspection
Operators take pride in maintaining robotic arms, meticulously cleaning away dirt, grease, and weld spatter that could compromise precision. This isn’t just routine maintenance—it’s a commitment to excellence.
Step 3 - Eliminate Contamination Sources
Operators go beyond surface fixes—they tackle the root causes of contamination, from poorly maintained wire feeders to clogged gas nozzles. By proactively identifying and resolving these issues, they ensure consistent weld quality, reduce downtime, and keep production running at peak performance.
Step 4 - Set Standards for Lubrication and Inspection
Operators take a proactive role by establishing precise lubrication procedures for robotic joints and conduct thorough inspections of electrical connections, preventing wear and potential malfunctions.
Step 5 - Conduct Routine Inspections
Through regular checks, operators become the first line of defense against costly breakdowns. By detecting abnormal vibrations or misalignments in the welding arm early, they prevent minor issues from turning into major repairs.
Step 6 - Standardize Visual Maintenance Tools
Color-coded tags and visual guides serve as constant reminders for operators, ensuring no critical maintenance task is overlooked. They help pinpoint exactly when consumables like contact tips or gas diffusers need replacing, streamlining workflows and preventing disruptions.
Step 7 - Drive Continuous Improvement
Feedback from inspections isn’t just collected—it’s actively used to refine and improve maintenance practices. Every insight helps shape a more efficient and reliable system, allowing operators to stay ahead of potential issues and continuously enhance performance.
Learn More
For more insights into TPM strategies and their benefits, visit Lean Production’s TPM Framework
And that’s your Corvex Connected Workforce Quick Take
At a welding facility in Dayton, Ohio
An operator noticed inconsistent wire feeding during an Autonomous Maintenance check of robotic MIG welders.
Following are the seven steps of AM he followed
1
The operator increased his knowledge of how the welder works
2
He cleaned the wire feeder system
3
He inspected for contamination sources
4
He replaced worn components based on established standards
5
He carried out inspection and monitoring
6
He then documented his findings using visual tools
7
He suggested improvements to prevent future issues
Today, high performing operations leaders in the metals industry are diligently deploying technologies that support TPM initiatives like Autonomous Maintenance.
Learn more about Autonomous Maintenance from the
Kaizen Institute.
Contact Corvex
Connect Your Workforce Today
Contact Us
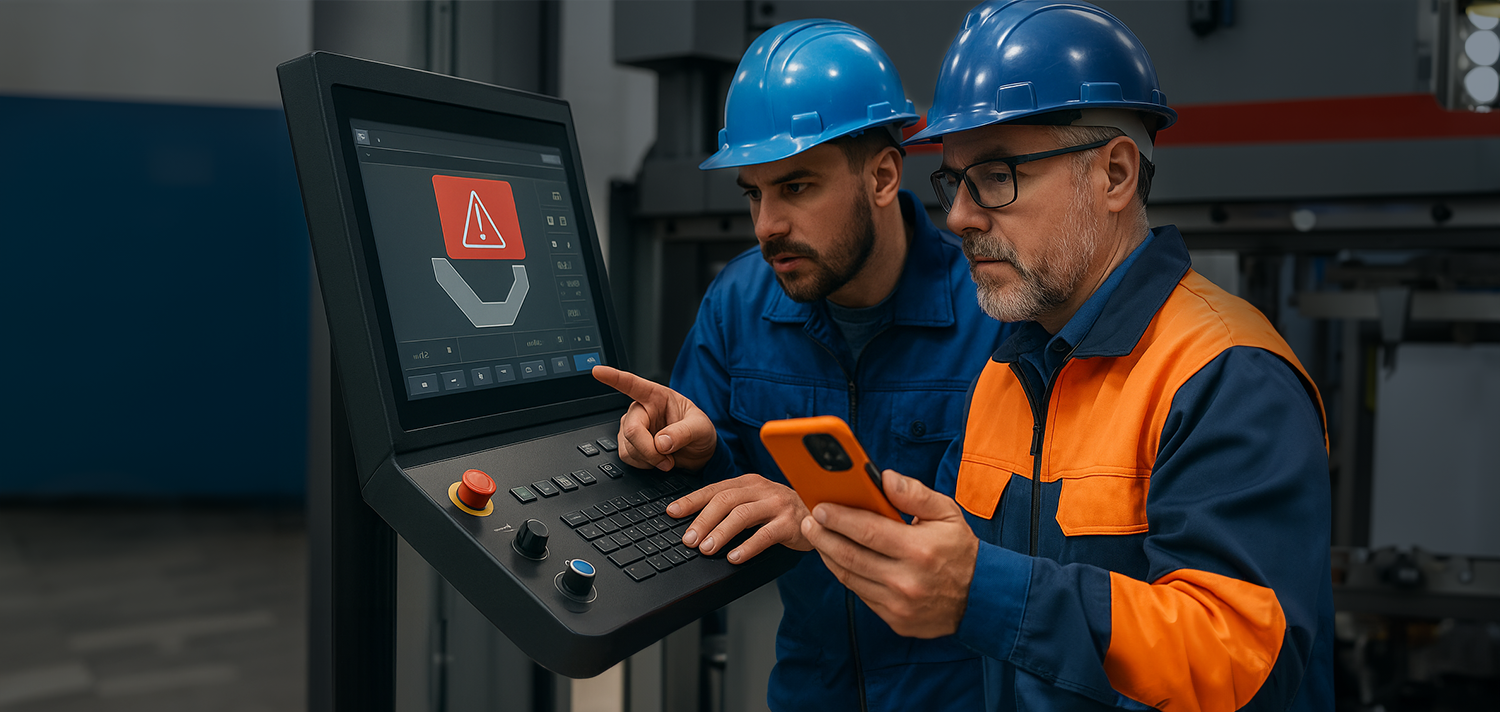
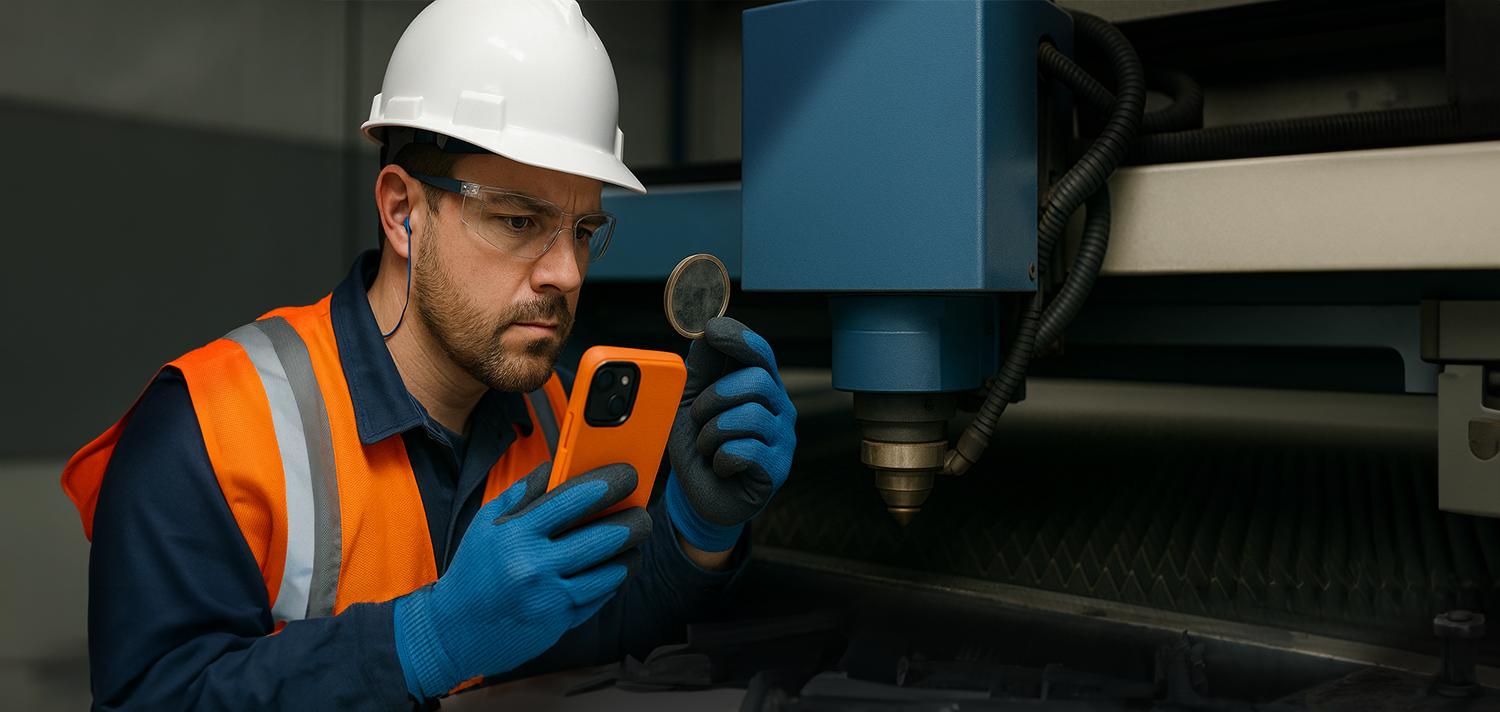
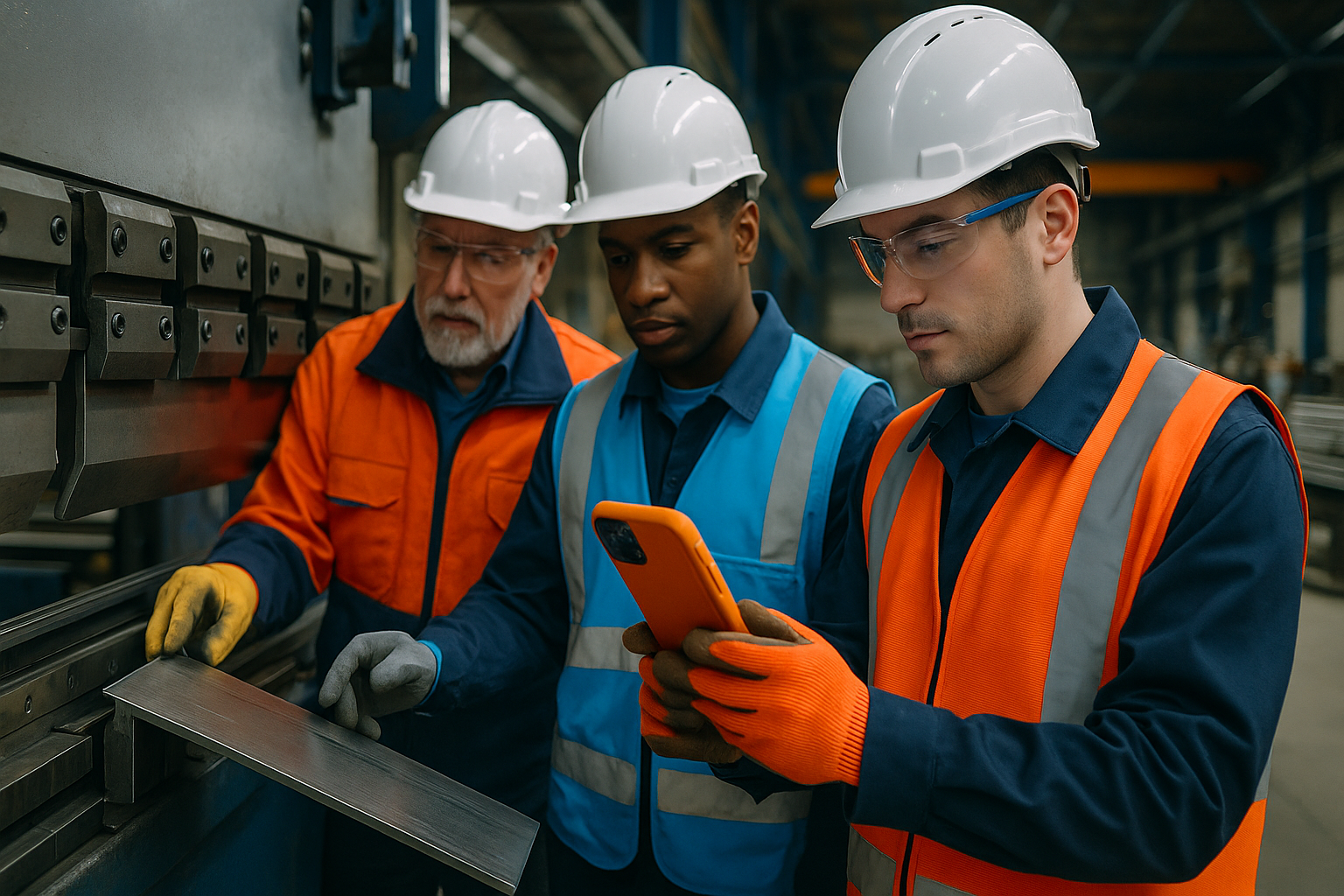
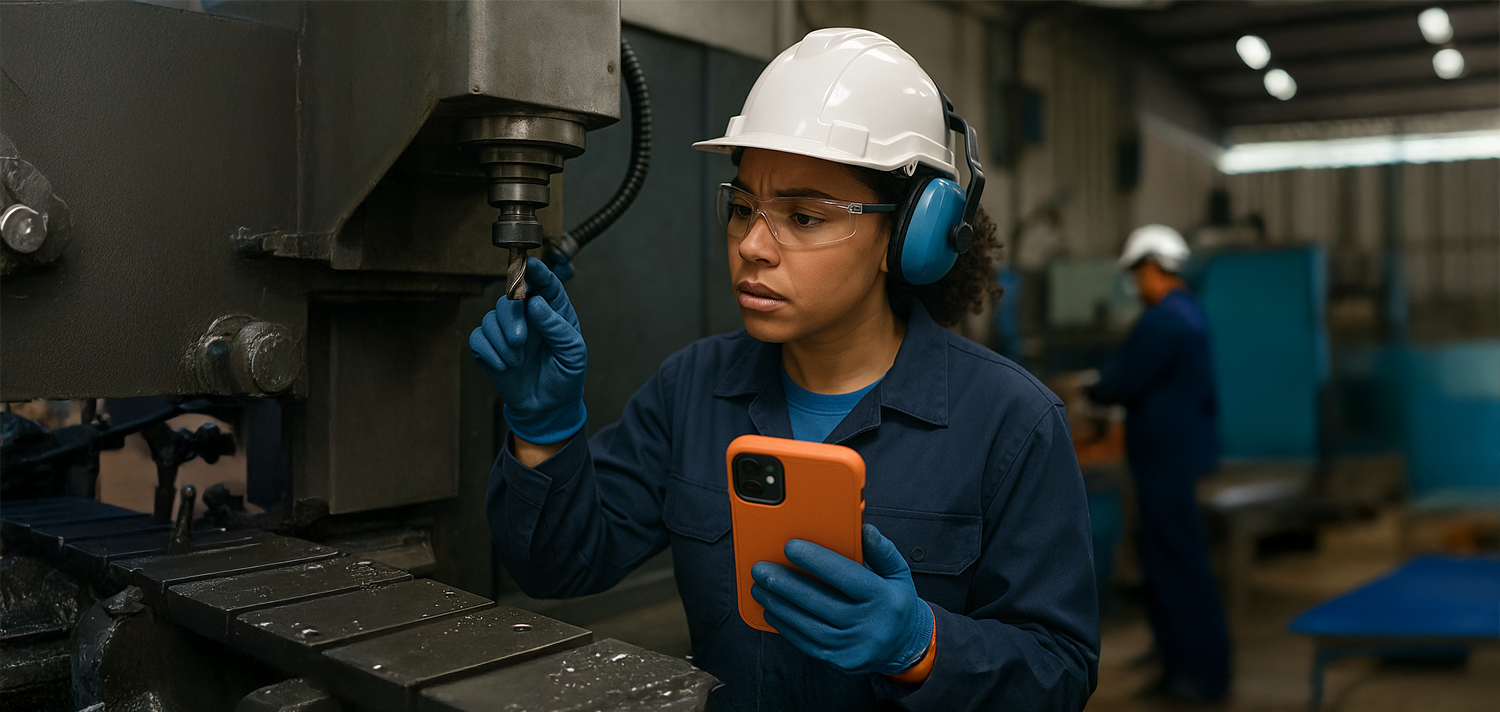
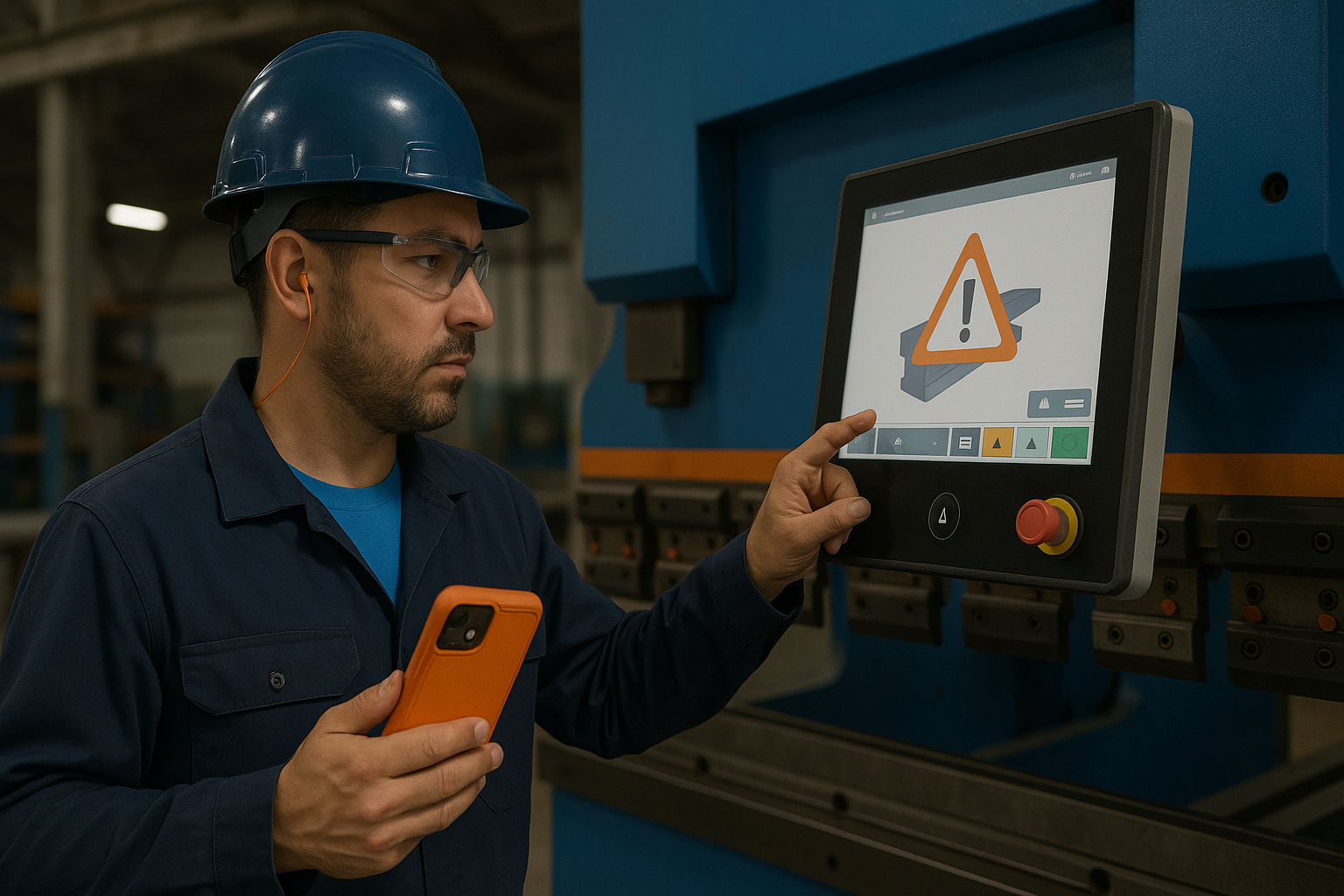
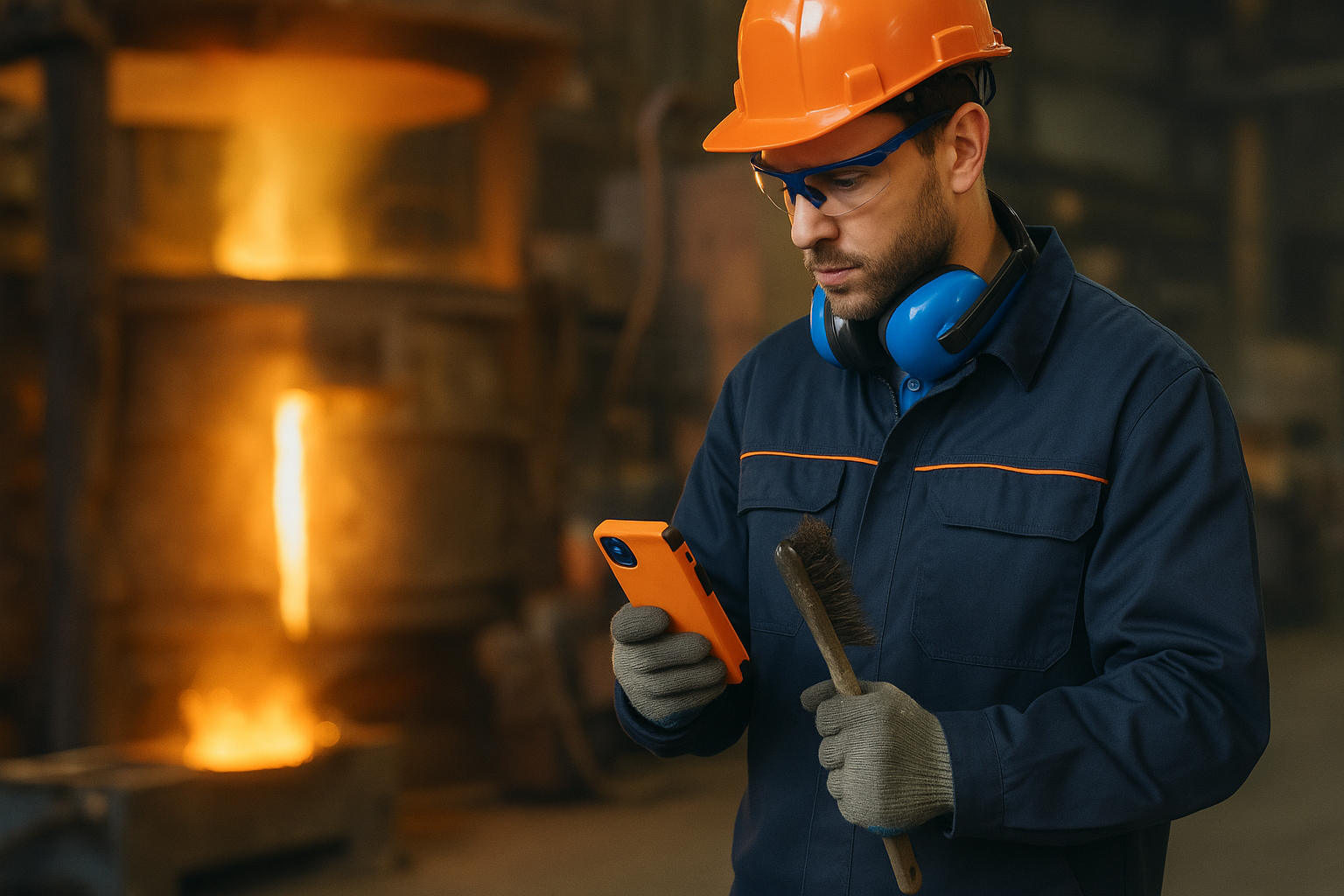
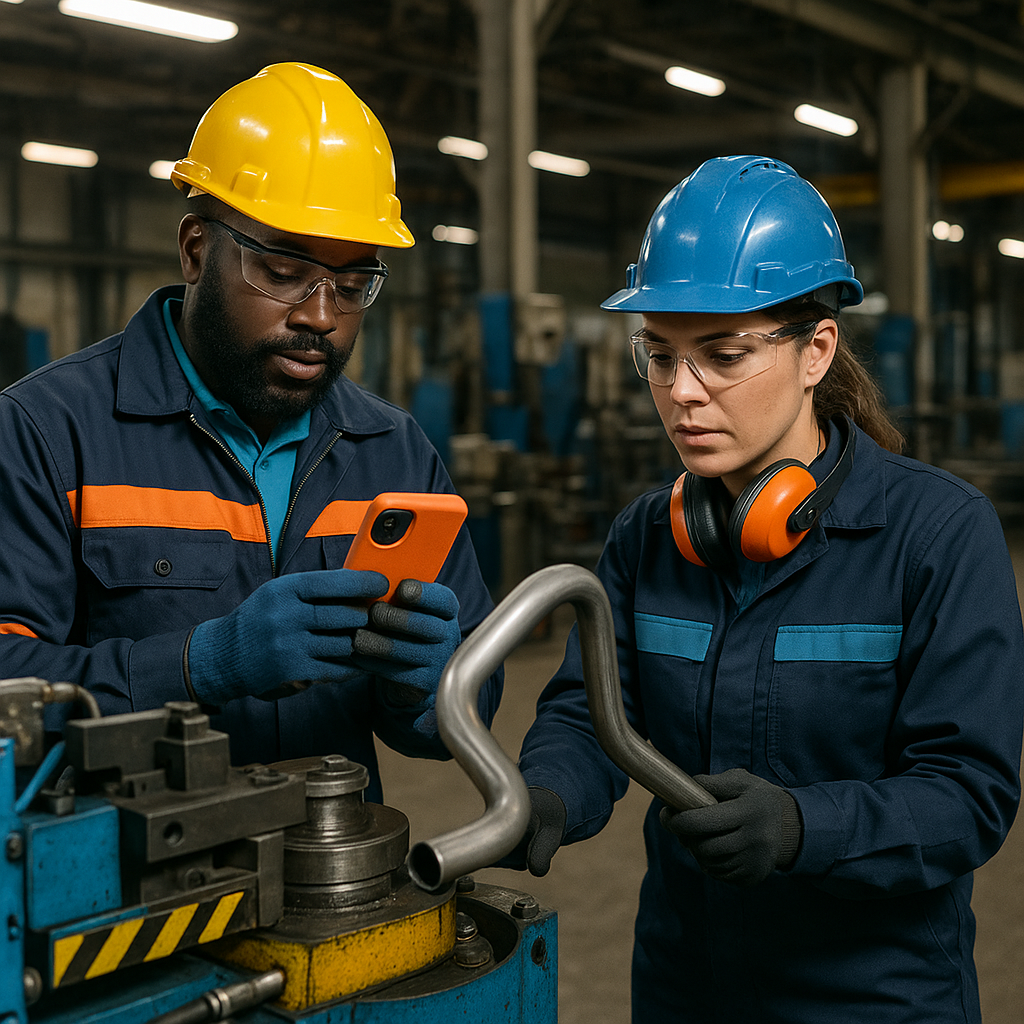
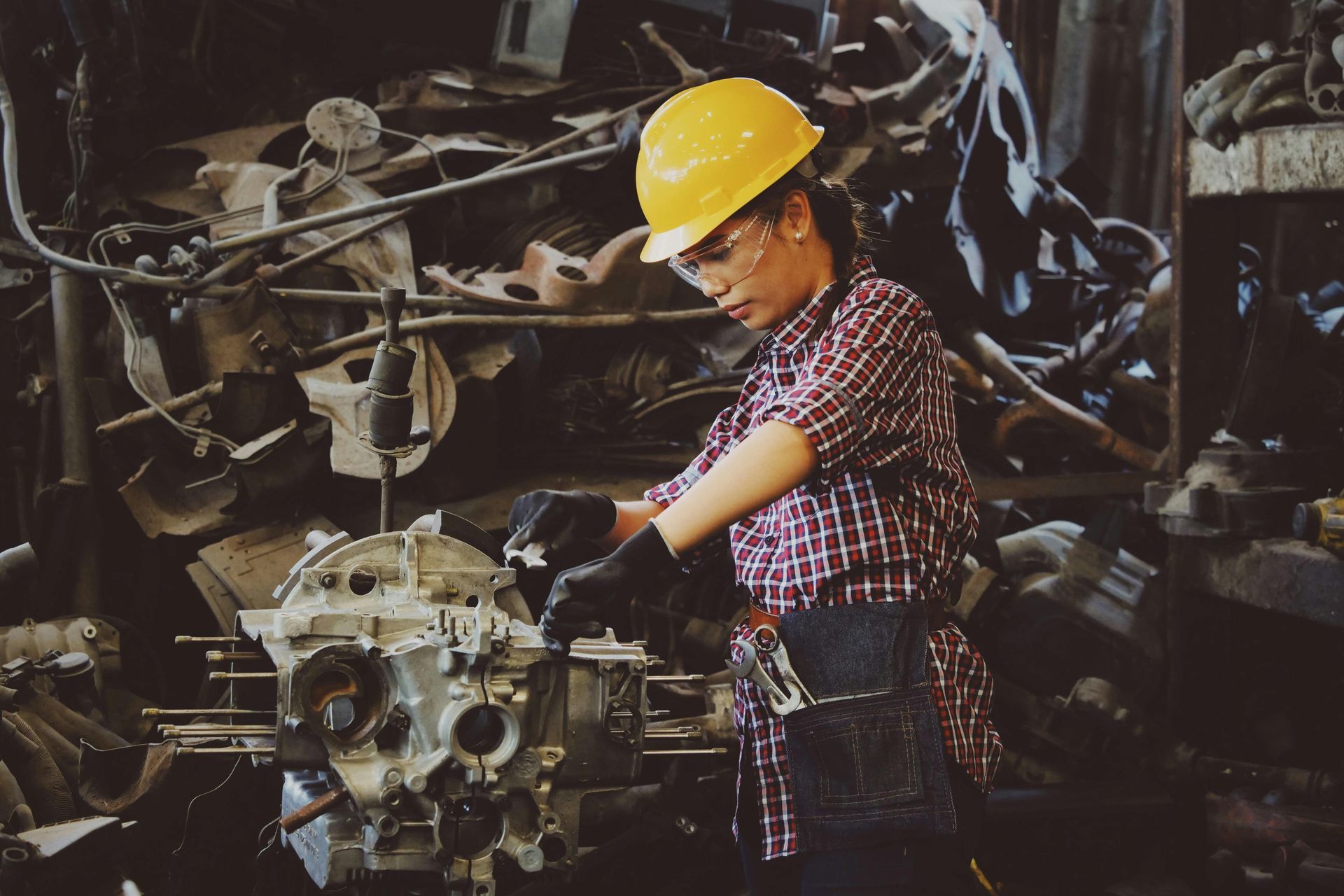
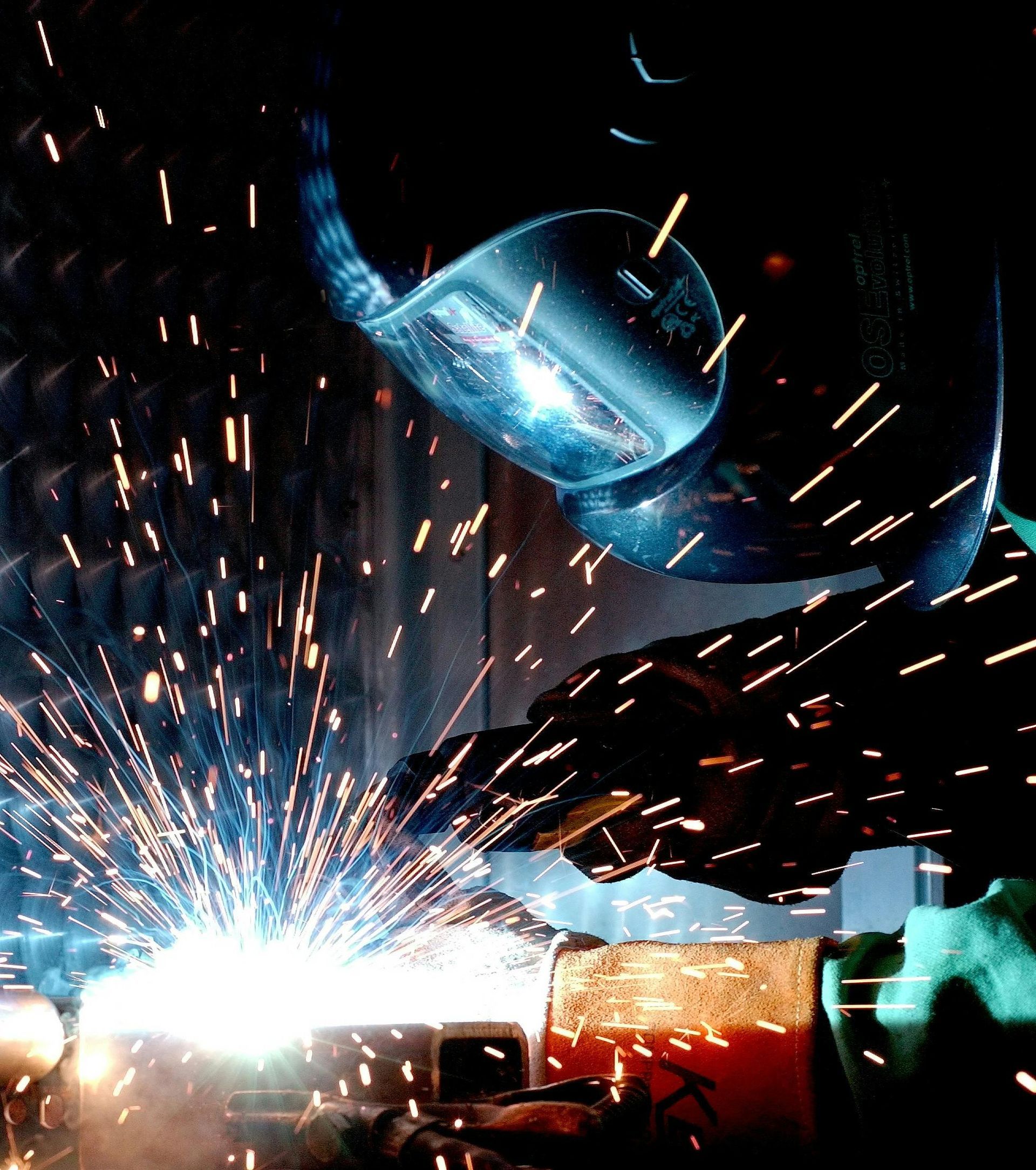