How Planned Maintenance Reduces Unplanned Downtime and Equipment Failures in Metal Manufacturing
Whether you're managing CNC machines on the factory floor or coordinating teams in heavy metal manufacturing, Planned Maintenance (PM) is a critical practice that keeps operations running smoothly. As a key pillar of Total Productive Maintenance (TPM), PM helps reduce unplanned downtime, extend equipment life, and control costs.
The Challenge of Unplanned Downtime
Unplanned downtime is one of the most significant challenges faced by metal manufacturers. Equipment failures not only disrupt production schedules but also lead to costly repairs and lost revenue. lubrication, inspections, and minor repairs. Unplanned downtime costs industrial manufacturers an estimated $50 billion annually (WSJ/Emerson).
This is where Planned Maintenance (PM) comes into play. PM involves scheduling regular inspections, preventive maintenance tasks, and repairs to address issues before they escalate. It’s a proactive approach that ensures equipment operates reliably and efficiently.
The Role of Planned Maintenance in TPM
Planned Maintenance (PM) is one of the eight pillars of Total Productive Maintenance (TPM). TPM is a manufacturing strategy designed to optimize equipment reliability, minimize downtime, and enhance product quality. PM focuses on scheduling maintenance activities systematically to prevent unexpected breakdowns.
Key Benefits of Planned Maintenance
- Reduced Unplanned Downtime: Regular inspections help identify issues early
- Improved Equipment Lifespan: Preventive care extends asset life
- Enhanced Productivity: Reliable machines keep production lines running smoothly
- Lower Maintenance Costs: Proactive repairs cost significantly less than emergency fixes
Real-Life Example: Aluminum Fabricator in Nashville
At a large aluminum fabrication plant in Nashville, Tennessee, a press brake operator implemented Planned Maintenance principles during daily checks:
- The operator noticed a gradual drop in hydraulic pressure through sensor alerts
- Reported the issue to the maintenance team
- The team replaced a worn-out press seal before it failed completely
This proactive intervention prevented an unplanned breakdown during a high-demand production period, reducing downtime for the press brake by 50% while improving overall equipment efficiency (OEE) from 70% to 76%. This demonstrates how trained operators can contribute directly to productivity and cost savings.
Benefits of Planned Maintenance
The impact of Planned Maintenance extends beyond individual success stories. According to a report by McKinsey, operations implementing PM experienced:
- 30% Maintenance Cost Savings
- Up to 50% reduction of Unplanned Downtime
Additionally, reactive maintenance can cost three to four times more than preventive and planned maintenance
(Powerhouse Dynamics).
Maximizing Uptime with Planned Maintenance
Operations leaders across the metal manufacturing industry are increasingly adopting Planned Maintenance strategies as part of their TPM programs. By proactively addressing equipment issues before they escalate, manufacturers can achieve:
- Reduced downtime
- Improved reliability
- Enhanced safety
- Lower costs
Learn More
For more insights into TPM strategies and how Planned Maintenance supports operational excellence, visit
Lean Production’s TPM Framework
And that’s your Corvex Connected Workforce Quick Take!
Contact Corvex
Connect Your Workforce Today
Contact Us
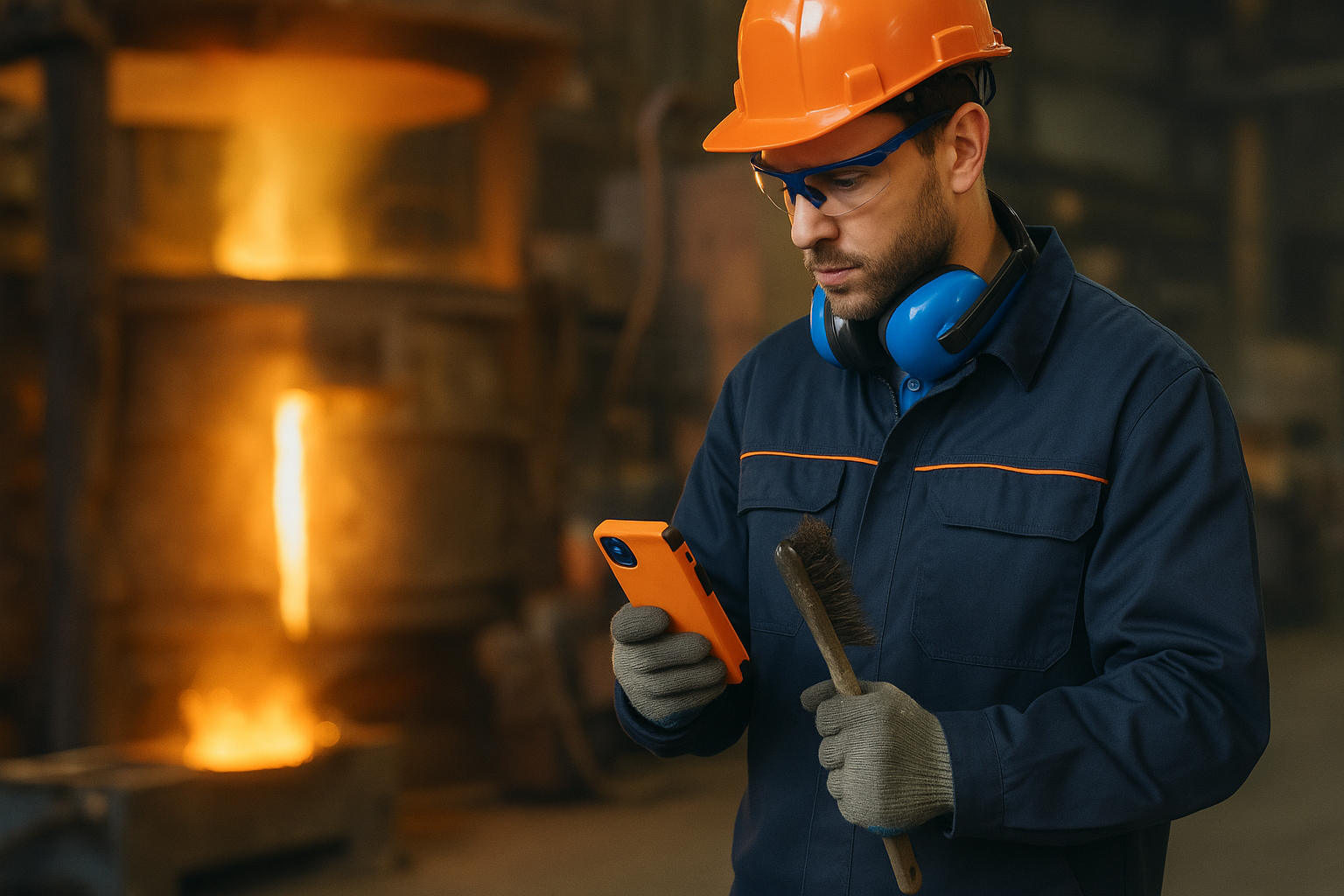
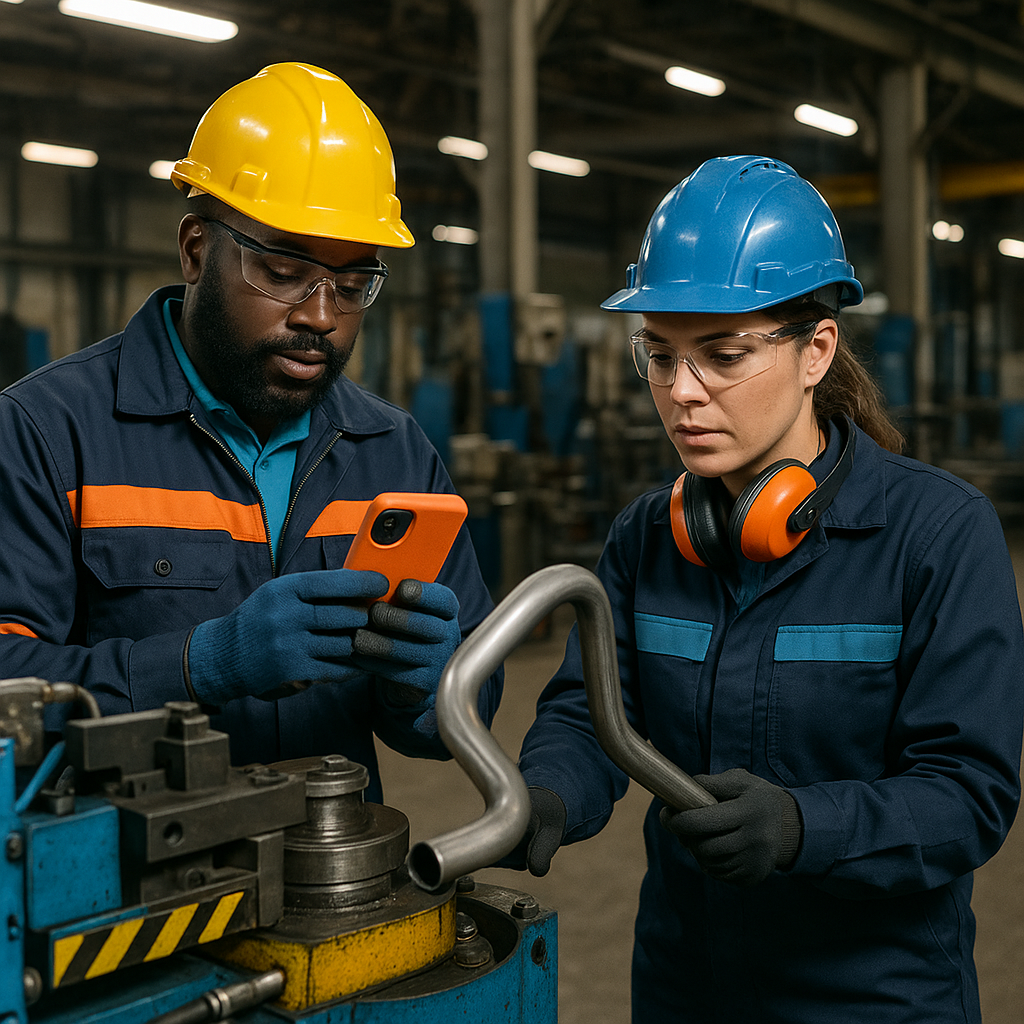
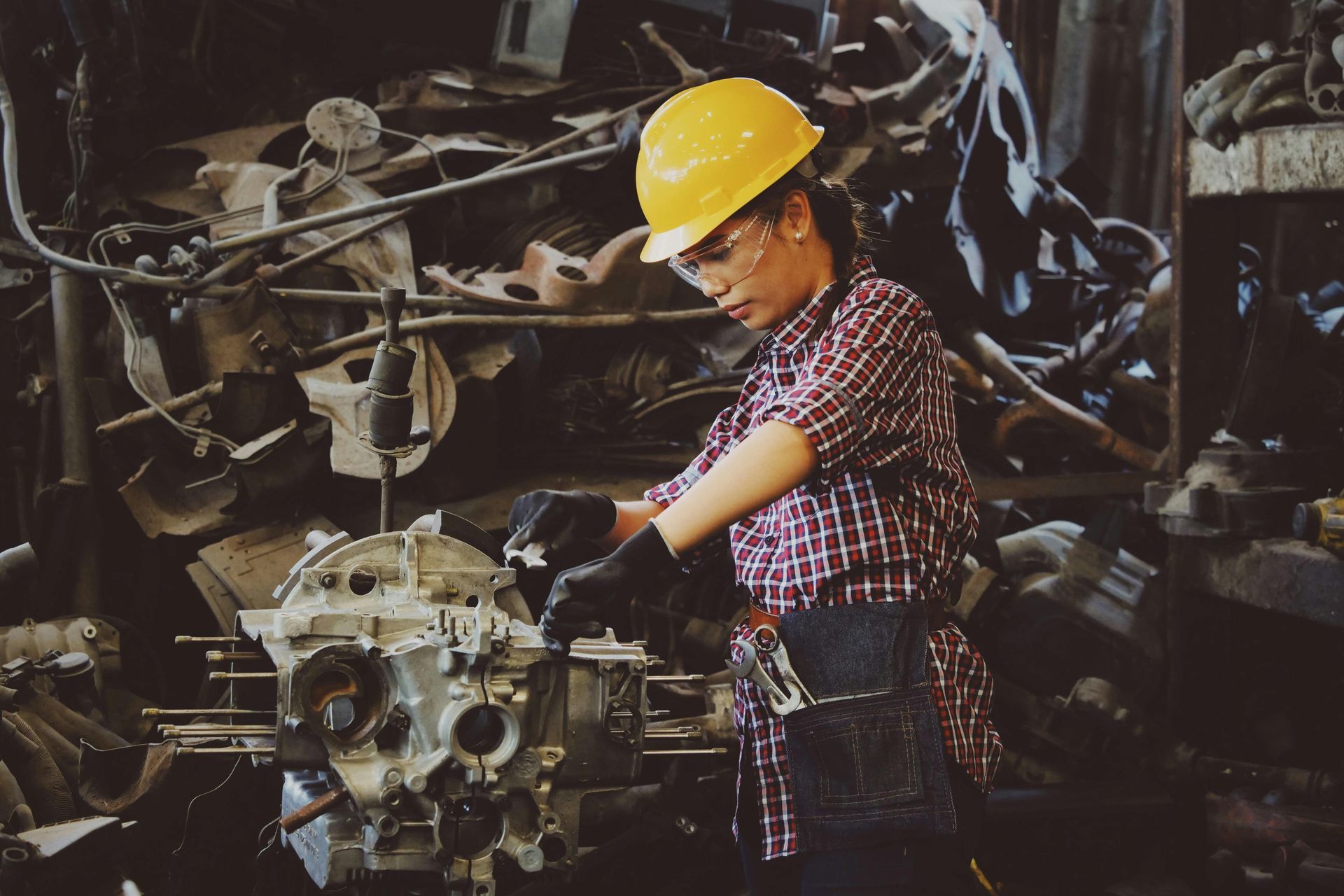
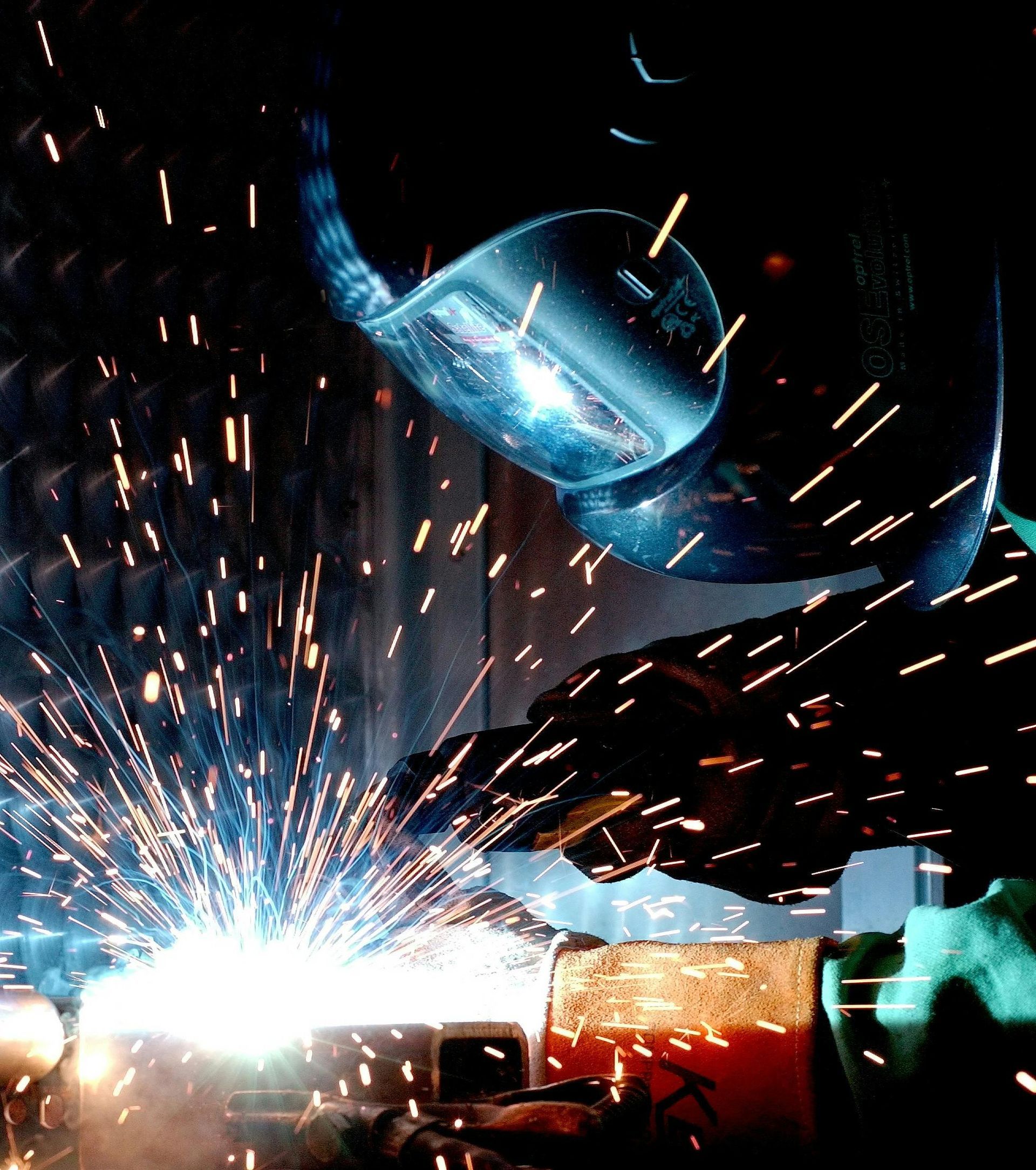